Worldwide collaboration has helped us rapidly respond and lead the way to recovery.
At Coats we understand that there are many uncertainties during this time concerning the COVID-19 (coronavirus) outbreak, including how we manage the health and safety of our employees. Our top priority is how we maintain strict adherence to the health and safety procedures and practices we have put in place for those employees working within our manufacturing facilities.
We already have an established culture of health and safety within Coats that is globally implemented across all our locations. At Coats we recognise that we are an essential company and so the safety of our workforce is paramount to us and to ensuring business continuity. We continue to be vigilant in our preparedness, prevention, response, and recovery efforts. Our first and foremost priority has always been, and will continue to be the health and safety of our employees, their families and the communities in which we work and live.
Like many companies, Coats has a comprehensive Pandemic Response Plan which was activated to help mitigate the transmission of the virus and ensure business continuity. Our plans and actions meet or exceed guidelines and restrictions set out by local, federal and global agencies. This approach allows our locations to continue safely producing essential products. [At Coats we’re different, you can rely on us and here’s why.]
At Coats we are looking at the science surrounding the pandemic, learning from all round world, our own experiences, at what are other governments doing so we are in a good place to make informed decisions. We are not simply following one counties mandates on how to tackle this, we look at best practices globally and learning so we can craft and steer our response to the global pandemic accordingly.
We implemented our global approach and started treating this as a pandemic weeks before it was declared a global pandemic. OSHA, the Guidelines for Employers, were implementing their guidelines around COVID-19 late March 2020, whilst as a business we were already meeting all of these new regulations. So the aftermath of this was that there was no impact on our business; as we were already doing all the right procedures before they were requested from us. We implemented a global plan for all employees in manufacturing plants to wear face masks on the 8th of April, a whole 3 months before the WHO and the CDC said everybody needs to wear masks.
We have implemented a Pandemic Response Plan to reduce the transmission. The prevention, preparedness, response and recovery (PPRR) model is a comprehensive approach to risk management. All Coats’ locations are following the plan based on the PPRR model and are implementing the same preventative actions. Early on, we adapted our plan based on the widely accepted and proven international PPRR model, we set out our objectives around each of these phases. This was adapted into the Coats crisis management model.
Pandemic Response Plan
COVID-19 Task Force Committees were established at site, cluster and global levels to:
- Monitor government actions and regulations
- Action daily meetings to ensure health and safety plans are being implemented
Group standard procedures have been established, which includes the following:
- Working from home
- Disinfection and sanitisation of sites
- Mandatory wearing of face masks
- Measurement of temperature on entering sites
- Travel restrictions
- Managing cases of infection

Rajiv Sharma, Group Chief Executive said: ‘Health and Safety is core to Coats and has always been our top priority. During the pandemic, we extended our COVID-19 prevention actions beyond employees to include their families and communities in which they live. I am proud of the way Coats responded to the disruption and challenges caused by COVID. The speed and scale of our comprehensive actions has been unprecedented. Empathy, compassion and care along with the use of science, data and technology characterised our response since the beginning of the pandemic.
‘It has not been easy, but the organisation has pulled together with grit, determination and confidence. We proactively sourced healthcare PPE across the world, delivered 200,000 hours of training, organised medical and wellness campaigns, invested in touchless technologies in our factories, developed an app to track and trace and isolate COVID cases, ensured appropriate medical care for serious cases and hired more doctors and nurses to go into communities. During this period, we have donated 60 million feet of thread for manufacturing millions of face masks.
‘Our focus has already shifted to winning the recovery. In a crisis, customers depend on trusted and dependable partners like Coats that offer quality, reliability, innovation, sustainability, digital solutions and technical support. Our global scale has allowed us to reliably deliver products and services to customers, resulting in incremental customer wins. We have seen an acceleration of digital adoption and sustainability in our industry and our recent investments in these areas have resulted in commercial gains during the period. Coats is focused on seizing the short-term and longer-term opportunities that are presented, and I am confident that we will emerge even stronger and more valuable to our industry in a post-COVID world.’
Coats factory global procedures have prevented the spread of COVID-19
At Coats our world class controls meet or exceed global practices. We are proactive, our measurement from a worldwide health and safety standpoint is one of prevention and proactivity versus reactivity and chasing injuries. We were one of the first companies to implement temperature screening, and we are continuing to fine tune and improve how we do this.
Our global risk mitigation procedures were implemented early for the safety of our employees. We continue to take the practices we had and really make them better, more efficient and apply them widely across Coats.
These practices and procedures include, but are not limited to:
Travel and visitor restrictions
Visitors are screened, provided with a mask if not wearing one and temperature checked before entering the factory premises

Vehicle entry procedures
Vehicles are sprayed both externally and internally with disinfectant

Temperature screening
Temperature screening prior to entry into our locations

PPE for employees
Proper respiratory protection and PPE is provided for higher-risk employees. A cloth face covering is required to be used by all other employees

Hand washing stations
Extra hand sanitising and handwashing stations have been set up throughout our sites

Increased disinfection
Increased disinfection with dedicated cleaning crews focusing on commonly touched surfaces

Social distancing
Social distancing in place throughout the factories and offices, including in break rooms, restrooms, meeting rooms, and manufacturing areas

Working from home
Working from home arrangements for any position not directly needed on the manufacturing floor

Utilising private transport
Private transportation arrangements both to and from work to avoid public exposure

Virtual meetings
Implementation of virtual meetings and postponement of any large gatherings

Staying home
Staying at home when sick and seeking appropriate medical care

Education
Continuous and ongoing education and training on COVID-19 prevention

Canteen
Tables are separated by 2 metres, acrylic separators are used for group tables and people are not facing each other

Prayer time
Clear markings on the floor to show what distance people need to keep away from others.

Meeting Rooms
Reduced number of chairs and reorganising chairs and tables according to social distancing rules.

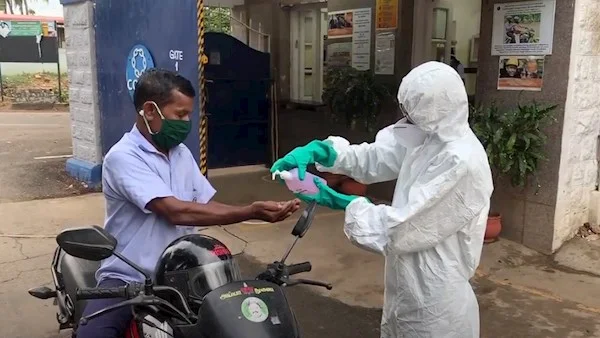
Coats Cares
Examples of other health & safety and wellbeing actions
At Coats our focus is on pro-active prevention activities, because Coats Cares about their employees and their families. In 2019 we initiated our company wide ‘Journey to Zero’ strategy with events and activities held at sites across Coats focused on health, wellbeing and safety. As part of the events, sites were asked to discuss and address their top risk areas to help prevent injuries arising from them. Events and activities such as these are important because they focus on the preventative actions we are taking to help us on our Journey to Zero. We tracked the number of improvement/preventative actions that have taken place so far to continue in our global health and safety initiatives.
We have in place global initiatives such as Safety Leadership training, cloud based incident reporting, implementation of CCTV across plants and standardised hazard identification processes across all regions. We have a solid framework of hazard identification, hazard control and risk management which was firmly in place before the global pandemic, and so these controls allowed us to be proactive in our response and ensure the right procedures were in place earlier than a lot of other big businesses.
As we have demonstrated good controls inside our sites to prevent the spread of the virus and we also need to focus on our protection outside Coats.
We measure and track how our employees get to and from work because that’s important to us for them to travel to and from their workplace safely. Our concern for their wellbeing doesn’t start when they come in the gate, our concern begins the moment they leave their house to the moment they get home. Our goal is to make sure they get home safely. Safety is the full circuit including while you’re at home. Global and local initiatives include, but are not limited to:
- Staying safe on the road
Provision of online road safety sessions - Safety marshals
Designated safety marshals monitor compliance with H&S - Keeping the families of our employees safe
Regular COVID-19 prevention awareness sessions for families
In addition to the COVID-19 measures that we have implemented, we continue focusing on safe working practices, continue near miss reporting and taking all the preventative actions to reduce incidents. Because Coats Cares.
Managing outbreaks
The preventative measures that we have in place throughout our factories is world class, demonstrating that above all else we care about our employees’ safety. We have sent people home and quarantined people that other businesses wouldn’t – because we care. Our approach to responding to a case inside, through the tracing or quarantining people, very few countries and government agencies are responding to it as well as we are. Coats is proactive, we are taking steps ahead of time to ensure a clear and effective set of procedures are in place for global rollout.
We have a standard approach to managing potentially infected cases.
Our approach:
- Exceeds that of other companies and ensures that actions adhere to highly rigorous health and safety standards
- Is based on best practice models recommended by leading health organisations across the globe
- Helps to ensure that the workplace is the safest place a person can be, beyond their own home
In Summary
We have a comprehensive procedure for managing potential and actual COVID-19 cases should they surface anywhere across our global footprint. Essentially the early actions we took in response to the pandemic to protect our employees and their families, helped us to stay open and continue operations. Coats continues to strive to be an essential partner to our customers, supplying threads, yarns and zips globally and even contributing significantly to the global effort to manufacture PPE.
Additionally, we have leveraged our technological strengths and are now implementing Digital Contact Tracing for our employees. Our global practices inside Coats factories that keep the virus from spreading are highly effective, but if it does it come through our Contact Tracing immediately and efficiently addresses it so we aren’t required to shut down our manufacturing plants.
[The only time Coats has shut down a site is when government has mandated a wider spread lockdown of plants and in those cases we were one of the first ones to reopen because the government reviewed our controls and gave positive feedback. We have been inspected a multitude of times and not one time have we been shut down or had negative feedback on the way we are set up to respond to the pandemic – we are in fact told that the procedures we had in place were really good and allowed to open early.]
Our early, highly effective response to this crisis has prevented any transmission of the virus within our factories and has kept operational impact to a minimum. Our goal remains to ensure that our Coats manufacturing sites and offices are the safest and healthiest places that our employees can be at all times so that we remain focused on success for all our stakeholders.
We have re-envisioned how to operate efficiently and how to continue business in spite of COVID-19 not in response to COVID-19.