It is changing the way you look at reinforcement materials and helps you say goodbye to the limitations of conventional manufacturing methods.
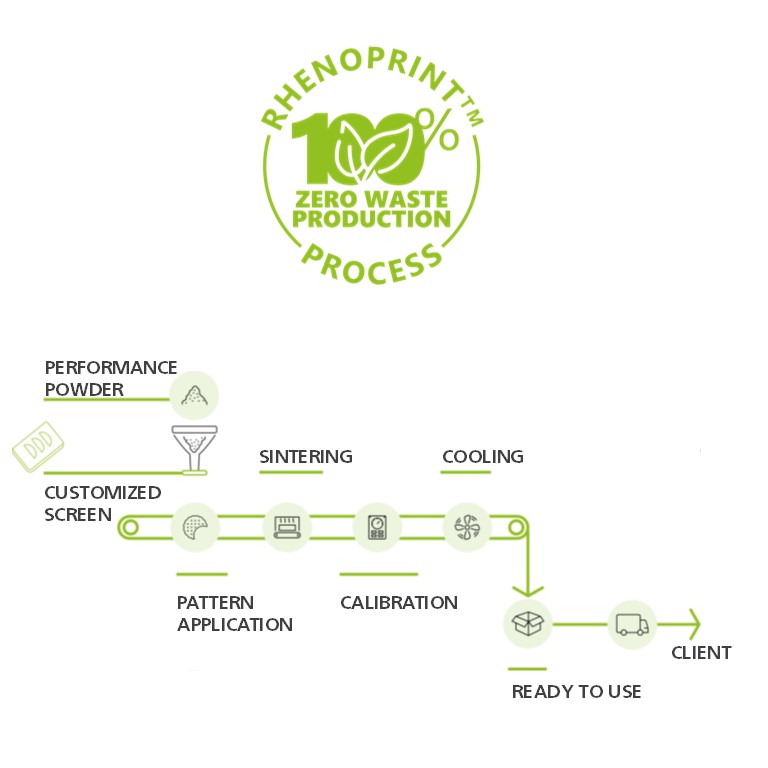
CUSTOM-MADE AND READY TO USE
Using this innovative Rhenoprint™ Process, we can create tailor-made reinforcement solutions – such as heel counters and toe boxes – that perfectly match your unique requirements. With Rhenoprint, customisation knows no bounds.
In practice, this works quite simply: You provide your individual cap shape and specification values, and Rhenoflex produces, able to realize almost any shape. With Rhenoprint, customisation knows no bounds. Whatever the shape, thickness, or hardness of material needed – anything is possible.
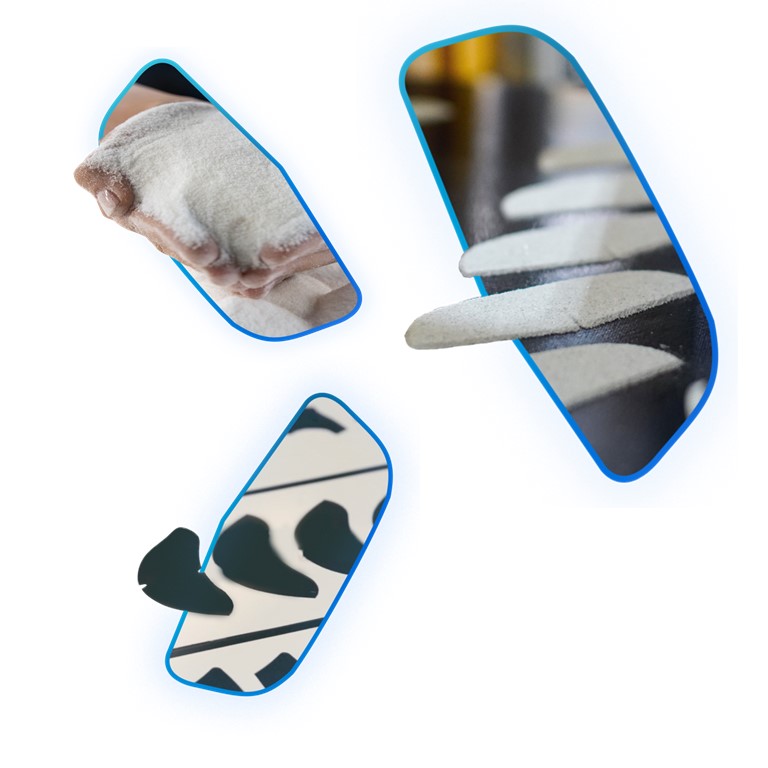
ZERO WASTE DUE TO PATTERN TECHNOLOGY
As customers provide us patterns that fits their needs, the Rhenoprint™ Process will be fully automized mass production. It also eliminates the need for any die-cutting or trimming, resulting in no waste. In addition, it requires approximately 30% less material than sheet stock.
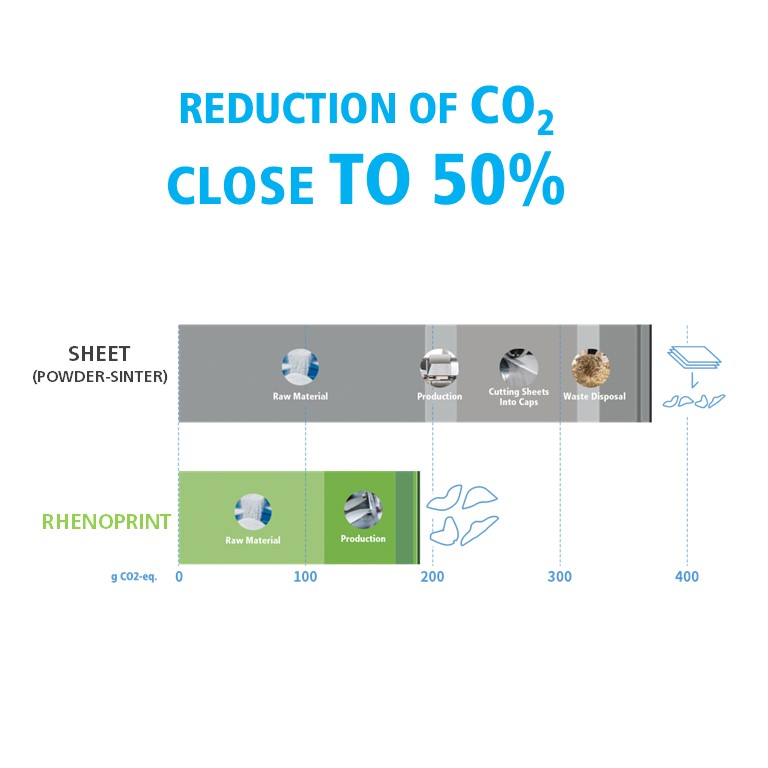
ATTRACTIVE CO2 FOOTPRINT
Compared to the Sheets (powder-sinter) from which reinforcement materials are cut, the punching and cutting process represents an additional energy-consuming and time-consuming step. Through the Rhenoprint™ Process, reinforcements can be instantly produced by “printing” customized shapes that precisely meet customer requirements down to the last millimeter. This unique production method boasts a 50% reduction in CO2 emissions compared to traditional comparable processes.
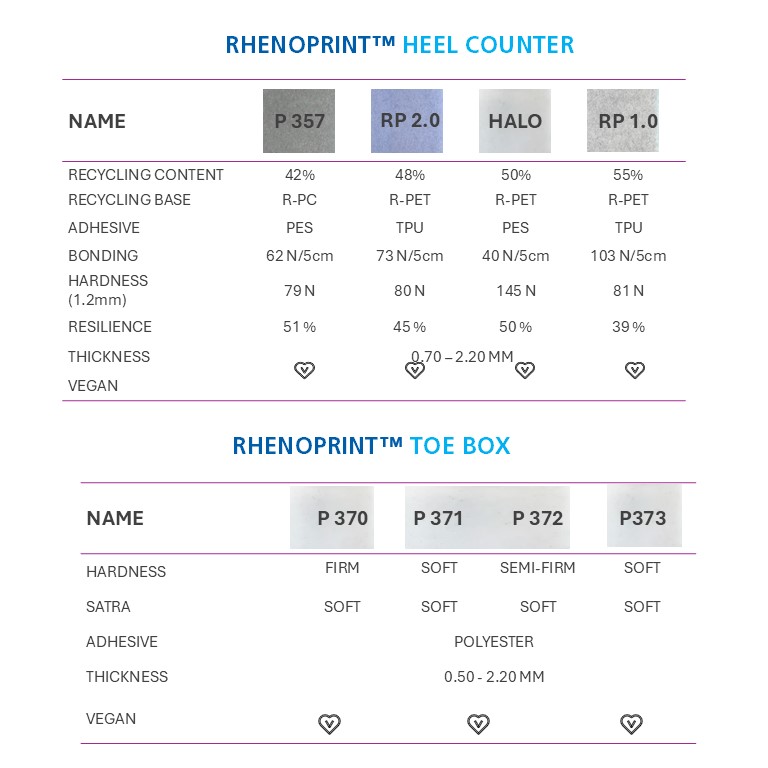
VARIOUS PRODUCT OPTIONS
In addition to our custom-made products, we leverage our extensive experience in reinforcements oroduction to offer a range of recommended products boasting diverse features, including recycled content, varied thicknesses, varying degrees of hardness, and resilience, all tailored to fulfill specific demands for diverse applications.
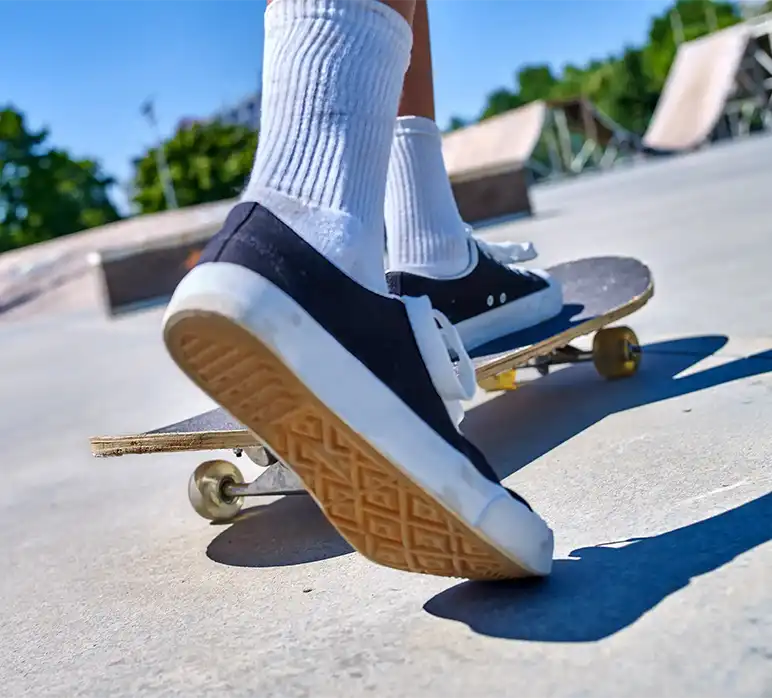
FEATURES AND BENEFITS
- Completely waste free production
- No cutting or skiving required
- Ready to use, eco-friendly and efficient
- Excellent CO2 footprint
- Unlimited customisation options
- Almost any shape, thickness or hardness possible
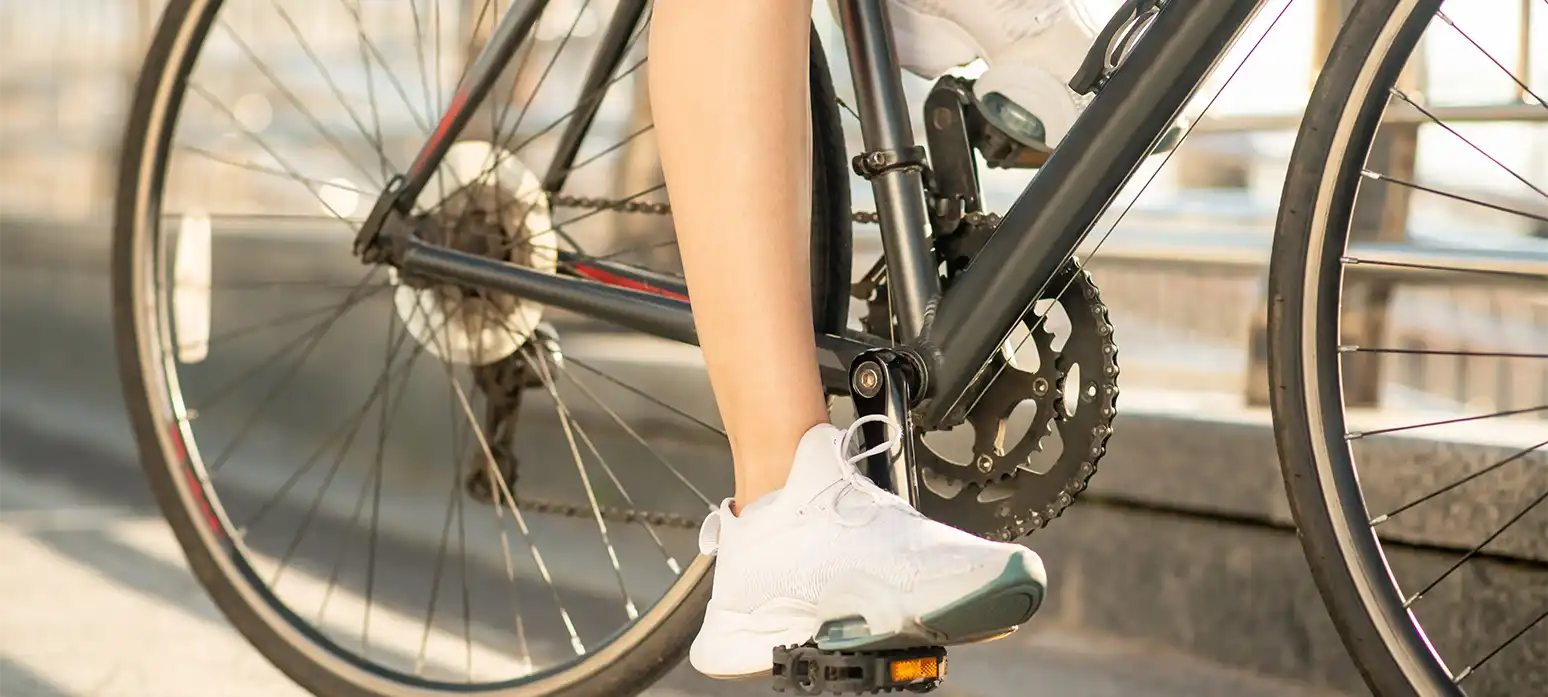
MAIN USES
- Sports Shoes
- Athletic / Sport / Sneakers
- Hiking Shoes
- Classic Shoes
- Outdoor / Workwear
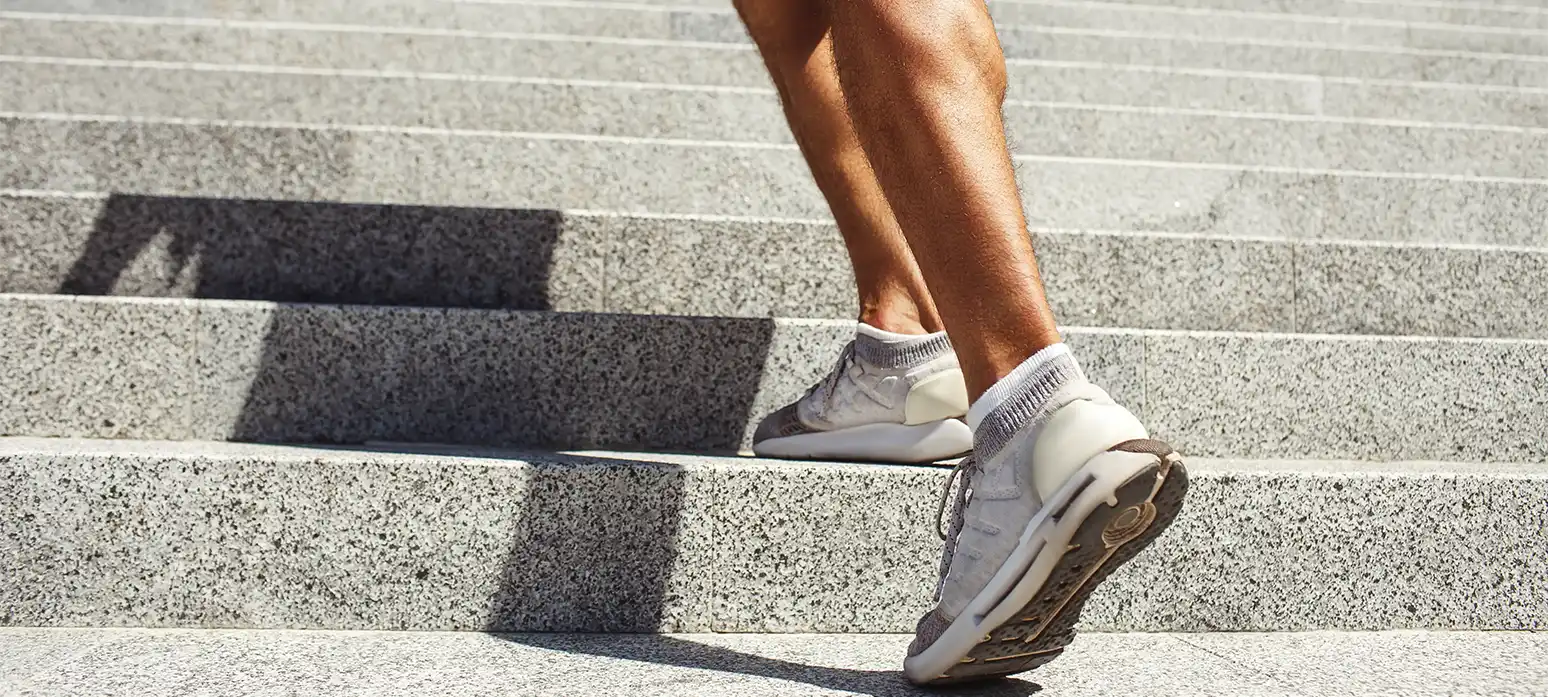
MAIN USES
- Sports Shoes
- Athletic / Sport / Sneakers
- Hiking Shoes
- Classic Shoes
- Outdoor / Workwear
OSTRZEŻENIE
Since conditions and applications vary considerably in the use of a product, the customer and/or user should assure herself or himself that the product meets end customer requirements and is suitable for the intended end use. Coats accepts no liability for unsuitable or improper use or application of products.
Information provided above is based on current averages and should be taken only as indicative. Coats accepts no liability for the preciseness and correctness of the information provided.
Product information sheets are updated from time to time, please be sure you are referring to the most recent publication. Coats supports customers with advice on individual applications on request; if you have any questions or concerns, please contact us.