SERTIFIKASI KEBERLANJUTAN KAMI
-
Registered users can place Bulk Orders . Contact local Coats office for registration.
Ikhtisar
Sustainability is at the very heart of our strategy at Coats. It encompasses the products we create and sell through innovation, as well as how we manage our operations. Our investment in sustainability, and leadership in sustainable innovation provides a strong competitive advantage with our customers.
The raw materials that we convert into finished goods contain more than 65% of our total value chain emissions and delivery of both our interim 2030 Scope 3 Science Based emissions reduction target and our 2050 Net Zero targets are contingent on us transitioning to materials with lower embedded emissions.
Mengelola sumber daya yang berharga secara bijak
Water is a critical resource used in many different ways, maintaining life on Earth and across our ecosystems, and is a key component across many industries. The textile industry is reliant upon water, using significant volumes throughout the industry’s dyeing and washing operations, adding to the demand from societies and countries in which we operate.
The United Nations recognises the importance of water through links to several Sustainable Development Goals, and at Coats, we continue to place water at the core of our sustainability strategy.
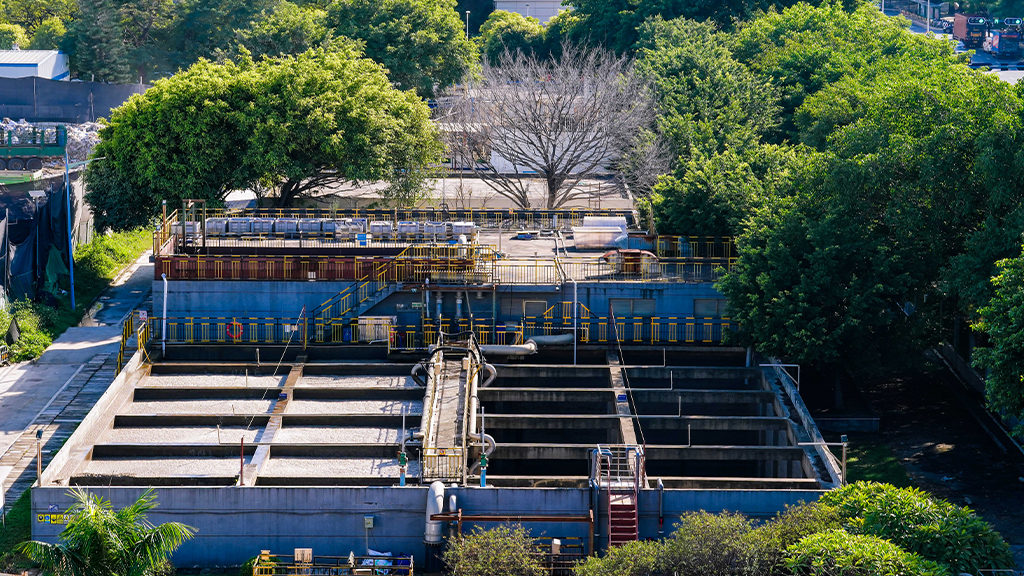
At Coats, we understand our need to manage water consumption responsibly, and actively drive two key metrics to support our journey to a sustainable operational future. While we remain committed to reducing our overall water intensity through a series of new and established initiatives, we have advanced further with our 2026 ambition to increase our water recycling rate by 33% (from a 2022 baseline).
In 2024, Coats saved 269,000 cubic metres of water across the group through continuous improvement initiatives, and reused a total of over 1 million cubic metres of water recycled from dyeing operations.
In 2024, 13 manufacturing facilities across the group now operate with water recycling capacity, recycling 1 million cubic metres of water this year, making up 27% of our total water consumption – a volume equating to over 400 Olympic-sized swimming pools.
Energi terbarukan untuk masa depan yang berkelanjutan
Achieving our material transition target is crucial for reducing our reliance on fossil fuels and lowering the overall environmental impact of our products. Lifecycle Analysis (LCA) plays a critical role in evaluating and guiding this transition.
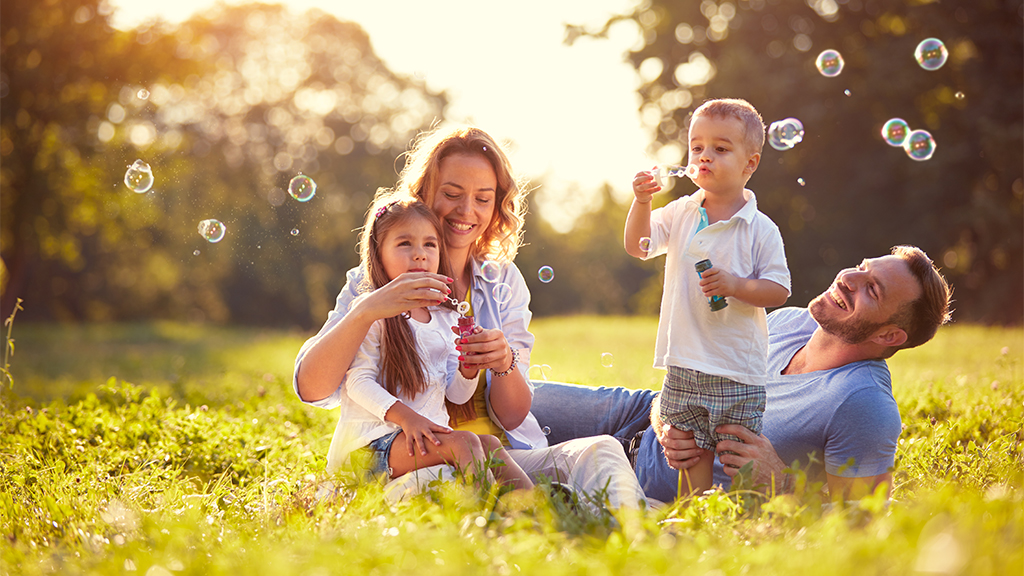
Through detailed lifecycle analysis, we can assess the sustainability benefits and trade-offs of recycled and bio-based materials, helping us identify the most viable alternatives that align with our climate goals.
Across all three of our divisions, our products are engineered to provide a guarantee of high product performance while minimising the use of raw materials and energy in the production process.
Melindungi planet kita
With our extensive global footprint, Coats has a responsibility to not only reduce the physical generation of waste materials, but also aims to prevent our wastes from having an impact on the environment and societies within which we operate.
In 2018, the Apparel division began their material transition and sustainability journey, aiming to shift from virgin to recycled thread products. This effort has led to increased sales from our Coats EcoVerde™ range of recycled products in 2024 – a 144% improvement in recycled thread sales over 2023.
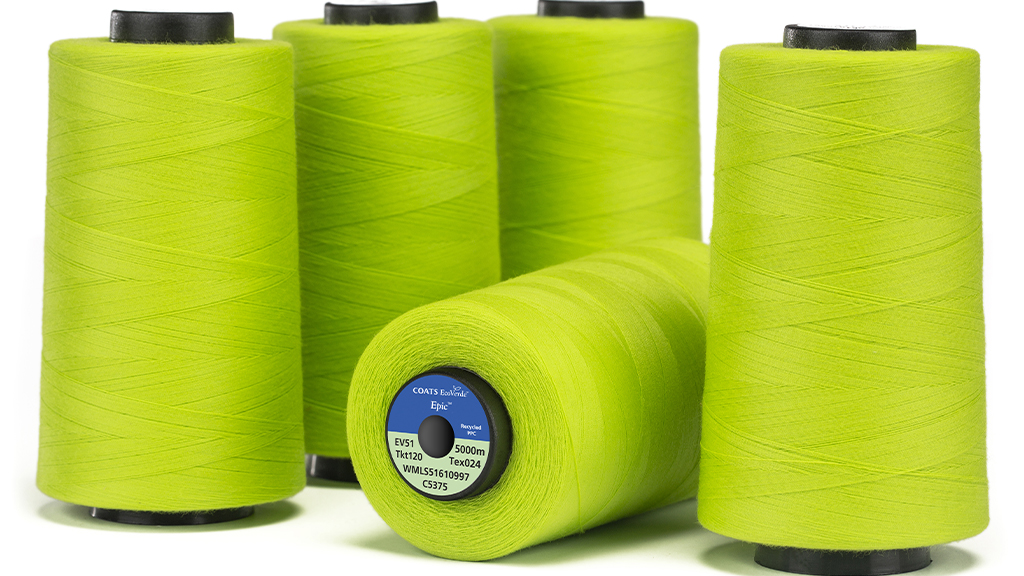
A key factor in this progress has been our systematic approach to transitioning virgin polyester substrates to recycled materials. By evaluating raw materials, qualifying suppliers, and establishing product specifications, we are ready for a complete transition.
Apparel: Pioneering leaders in customer value creation
Footwear: Market leader shaping the future of footwear thread and components
Performance Materials: Transforming the footprint for growth
Footwear: Market leader shaping the future of footwear thread and components
Performance Materials: Transforming the footprint for growth
Zero Discharge of Hazardous Chemicals
At Coats, we continued to deliver on our Effluent Compliance commitments which are focussed on eliminating hazardous chemicals from our supply chain.
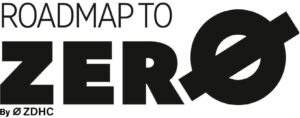
The core of this approach uses the Roadmap to Zero programme to assess chemical discharge compliance under the Zero Discharge of Hazardous Chemicals (ZDHC) framework. We extended the number of sites included in 2024, with 25 manufacturing units now in-scope.
Our primary control for ensuring effluent compliance is the governance of incoming chemicals through strict adherence to our restricted substances list which applies to all incoming raw materials. We work on the basis that by controlling raw materials at source, we can be confident of controlling the composition of effluent at the point of discharge. To further support the programme we refined our internal procurement processes, upgraded our chemical inventory and management controls, and delivered additional compliance-related Chemical Officer training programmes.
In 2024, out of 12,590 analytical tests against the framework, only 19 narrowly missed their minimum ZDHC foundational limits, delivering an effluent compliance level of 99.85%. This is an uplift from our 2023 performance levels and continues our year on year trend of annual increases in compliance levels. With tolerance limits tightening, and as we transition to recycled and bio-based materials, we remain proactive in mitigating risk from external and incidental contaminants entering our supply chain.
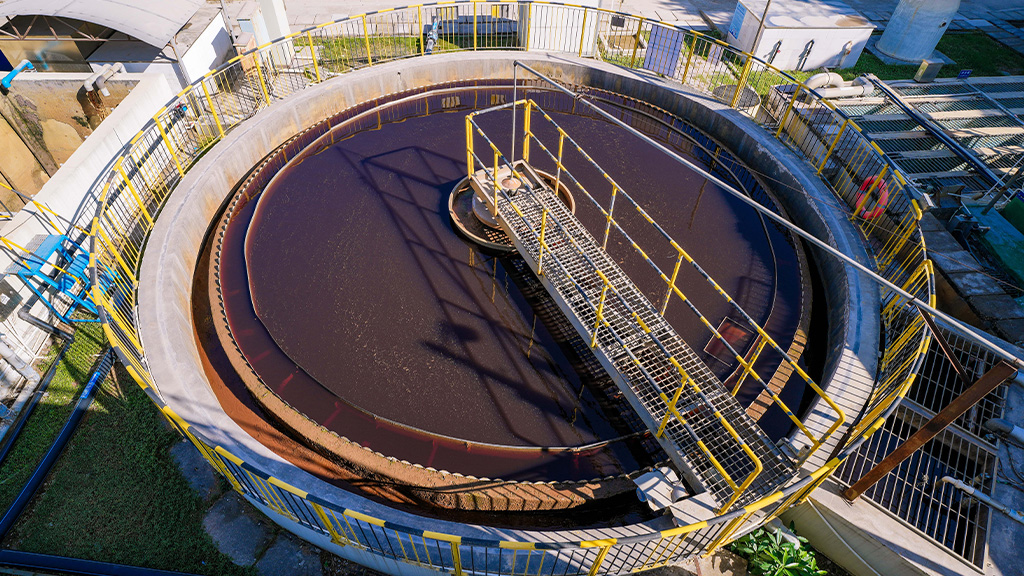
Through evolving internal controls, continued supplier collaboration, and the application of global investigative resources, we are confident of delivering sustained levels of compliance as we advance towards our KPI target.
We continue to monitor key effluent parameters (temperature, pH, chemical oxygen demand, biological oxygen demand, total suspended solids) via online sensor technologies for our direct discharge waste water treatment plants. Sites
with this capability are equipped with real-time dashboards and automated alerts which trigger in the event of any parameter approaching an out-of-tolerance measurement.
OEKO-TEX®
OEKO-TEX® standards enable everyone to make responsible decisions and protect natural resources.
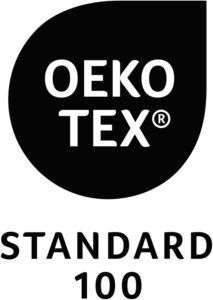
OEKO-TEX® STANDARD 100 is a label for textiles tested for harmful substances. It sets the benchmark for textile safety, from yarn to finished product. Every item bearing the STANDARD 100 label is certified as having passed safety tests for the presence of harmful substances.
At Coats, our extensive testing programme which ensures that all our finished goods thread products align to OEKO-TEX® STANDARD 100, Product Class I, internationally recognised as one of the principal benchmarks for textile chemical compliance.
We fully meet the requirements of REACH relating to presence of SVHC in our products. Inquire with our Coats representative on product with these certifications.
- Coats India — 08-689 | 11-50576 | 11-61192 | 11-69584 | 14038
- Coats India — 11-40291 | 11-61332 | 11-63158 | 11-39642
- Coats Indonesia — 11-36904 | 11-61548
- Coats Bulgaria — 11-33876
- Coats Bangladesh — 11-34931 | 11-63636 | 11-34526 | 11-63304
- Coats Group plc — 11-36001 | 11-37257 | 11-64846
- Coats Colombia — 11-39561 | 11-62848
- Coats Egypt — 11-21535 | 11-61091
- Coats Vietnam — 11-32686 | 11-62347 | 11-24395 | 11-24396 | 11-62362
- Coats Honduras — 11-67844 | 11-37710
- Coats Pakistan — 11-63584 | 11-29244 | 11-63889 | 08-7187
- Coats Morocco — 11-72274 | 11-38031
- Coats Mexico — 11-36192 | 11-40094
- Coats China — 11-60314 | 18046 | 11-36117 | 11-60660 | 11-68351
- Coats China — 11-36896 | 11-60254 | 11-36212
- Coats Thailand — 11-61506 | 11-39397
- Coats Sri Lanka — 11-64538 | 08-4377
- Coats Romania — 11-62943 | 11-37362
- Coats Turkey — 11-32734 | 11-62310 | 17092 | 11-46326 | 08-4812
- Coats Tunisia — 11-67885 | 11-40258
Restricted Substances List
We believe our Coats Restricted Substance Lists (both our Products RSL and our Manufacturing RSL) are the most stringent in the textile industry.
Our Restricted Substances List (RSL) programme ensures that our products do not present any risk to our customers and consumers and is actively managed with annual updates.
Application of our RSL is a core part of our Group Supplier Code
management as all inputs into our processes have to be certified as compliant to our RSL apart from a small number of industrial products with performance driven exceptions that are approved at senior management level.
Product safety
As part of Coats Product Safety programme, we require that all Coats’ suppliers of raw materials, dyes, chemicals and packaging materials meet the highest standards appropriate for their end-use. A comprehensive list of restricted chemicals is revised and reissued to all of our material suppliers every year.
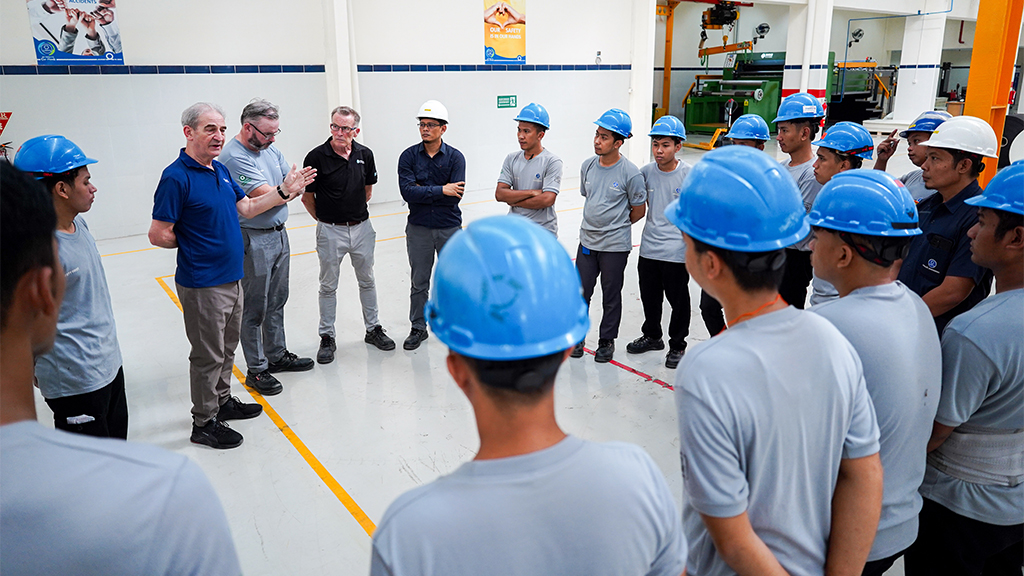
Effective chemical safety management is a cornerstone of our compliance programme. It ensures a safe working environment while mitigating risks associated occupational health and safety, environmental and product safety in all our finished
goods.
Coats MRSL
To ensure that our finished goods comply with all applicable global legislative requirements and industry standards we impose maximum permitted limits through our own bespoke manufacturing restricted substances list (MRSL) with which all our
suppliers of all raw materials, dyestuffs, chemicals and packaging must comply as a prerequisite to supply.
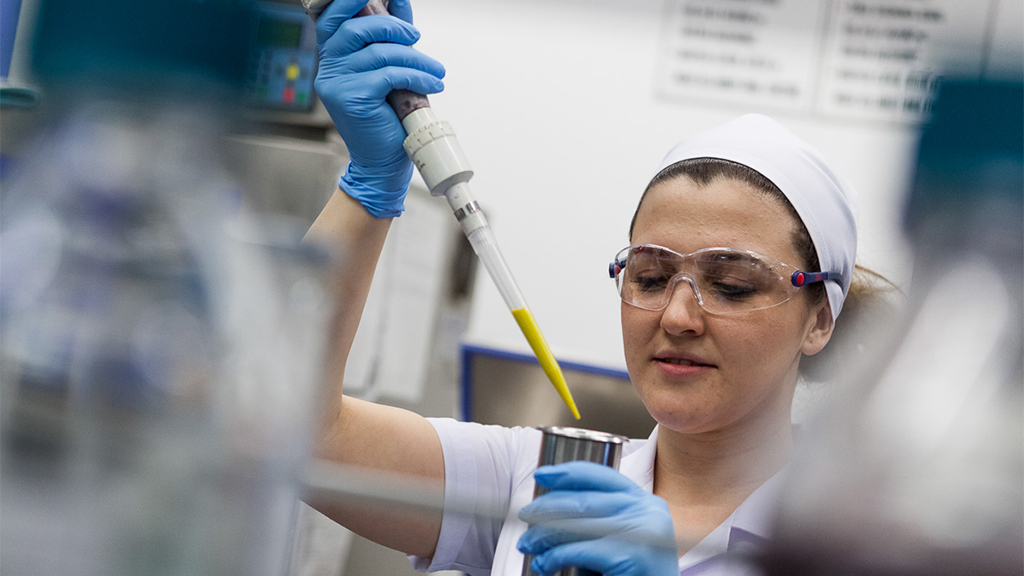
Our Apparel and Footwear MRSL comprises a comprehensive list of over 1100 chemical substances with limits that are, as a minimum, equivalent to those required by numerous extensive global regulations, those as stated in ZDHC MRSL v3.1 and those imposed by our customers own requirements.
Better Cotton™
Better Cotton is the world’s leading sustainability initiative for cotton.
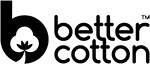
Our definition of preferred materials is based on “Preferred Materials” guidelines issued by Textile Exchange, which defines a preferred fibre or material “as one which results in improved environmental and/or social sustainability outcomes
and impacts in comparison to conventional production”.
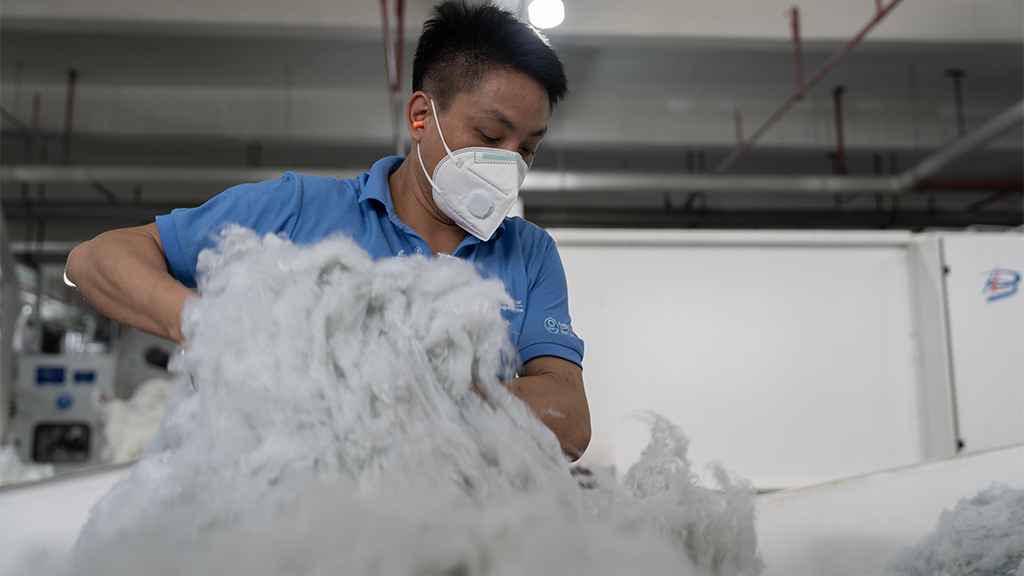
Our preferred materials are non-virgin oil-based and include recycled synthetic fibres, Canopy certified man-made cellulosic fibres, renewable materials like cotton, organic cotton, BCI Cotton and bio-based materials like Poly Lactic Acid (PLA).
Standar Daur Ulang Global
The Global Recycled Standard (GRS) is a voluntary product standard for tracking and verifying the content of recycled materials in a final product.
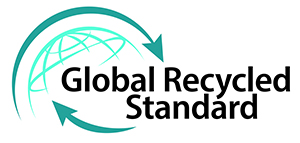
The standard applies to the full supply chain and addresses traceability, environmental principles, social requirements, chemical content and labeling.
GRS covers processing, manufacturing, packaging, labeling, trading and distribution of all products made with a minimum of 20% recycled material.
It also sets requirements for third-party certification of recycled content, chain of custody, social and environmental practices, and chemical restrictions.
Coats ensures that any facility that processed recycled materials is externally certified to GRS and that any recycled materials that we buy are certified so that we can provide fully certified recycled products.
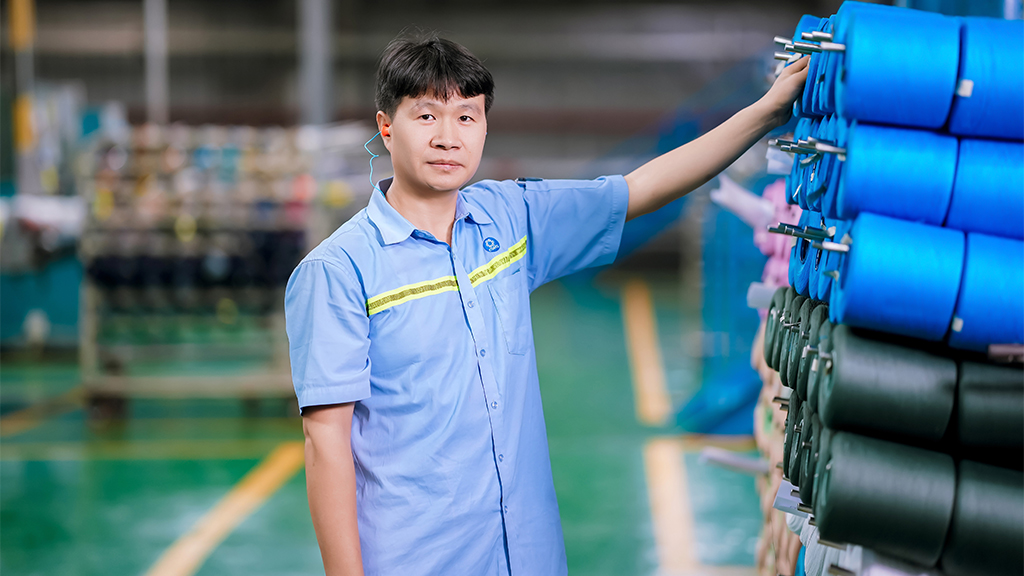
Global Organic Textile Standard
The Global Organic Textile Standard (GOTS) is an internationally recognized certification for organic textiles.
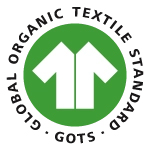
It ensures that the entire supply chain, from harvesting the raw materials to environmentally and socially responsible manufacturing and labelling, is compliant with stringent organic and ethical standards.
View/download Coats’ GOTS certificates by location below.
Higg Index
The Higg Index is a suite of tools developed by the Sustainable Apparel Coalition (SAC) to measure and improve the environmental and social sustainability of apparel, footwear, and textile products across the entire value chain.
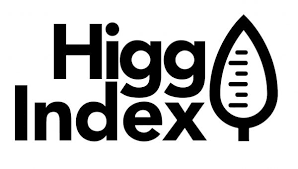
It’s not a single score or label but a modular system that companies use to evaluate different parts of their operations from raw material sourcing to end-of-life impacts. It helps brands, retailers, and manufacturers assess performance, identify hotspots, and make improvements.
Since 2017 Coats has adopted the Higg Facility Environmental Module (Higg FEM) to inform our existing and prospective customers of the environmental performance of our facilities. The programme, which in 2024 covered 32 of our units, includes a rigorous external assessment of our chemical management processes.
We utilise the results of this process to seek further improvements and to benchmark ourselves against the textile industry as a whole. This allows us to make better informed sustainable choices in respect to supply chain and facility performance. Access to this data is available from the Worldly platform.
Connect with Coats in Higg by logging in to view our verified and annual FEM report using Higg IDs for our locations below.
- Coats Bangladesh - Chittagong: 124937
- Coats Bangladesh - Dhaka: 140852
- Coats Bulgaria : 145803
- Coats China - Qingdao: 125472
- Coats China - Shanghai: 123706
- Coats China - Shenzhen: 33114
- Coats China - Tianjin (JYSC): 137565
- Coats China - Rx Dongguan: 140210
- Coats China - Tx Dongguan: 124528
- Coats Colombia - Pereira: 145906
- Coats Egypt: 50214
- Coats Honduras: 125574
- Coats India - Ambasamudram: 131332
- Coats Indonesia: 17752
- Coats Mexico - Orizaba: 125546
- Coats Morocco: 146097
- Coats Pakistan - Karachi: 145676
- Coats Pakistan - Lahore: 145675
- Coats Romania: 145933
- Coats Germany - Rx Ludwigshafen: 17746
- Coats Germany - Tx Möckmühl: 130121
- Coats Vietnam - Rx: 148039
- Coats Vietnam - Tx: 164242
- Coats Vietnam - Hanoi: 145723
- Coats Vietnam - Ho Chi Minh City: 122647
- Coats Sri Lanka: 130564
- Coats Thailand: 138105
- Coats Tunisia: 145970
- Coats Turkey: 123076
- Coats Italy - Tx Montemurlo: 168706
- Coats Italy - Tx Ripatransone: 130252
- Coats Group plc - Tx Skelton: 122523
Great Place To Work®
Great Place to Work® (GPTW) is an organisation which allows companies to quantify their culture and produce better business results by creating a high-trust work experience for all employees. Coats is partnering with GPTW since 2021.

In 2019, we launched our Sustainability Strategy including five pillars and seven targets to achieve by 2022. Social is one of the pillars and within that we aspire to achieve ‘Great Place to Work-Certified™ status for all of our key sites.
In the next phase of our sustainability journey, we will continue to utilise Great Place to Work as the primary barometer to measure levels of employee engagement and trust, and are committed to further enhancing our current percentage of employees covered with certification to 88% in 2026 and aspirations to achieve 90% by 2030.
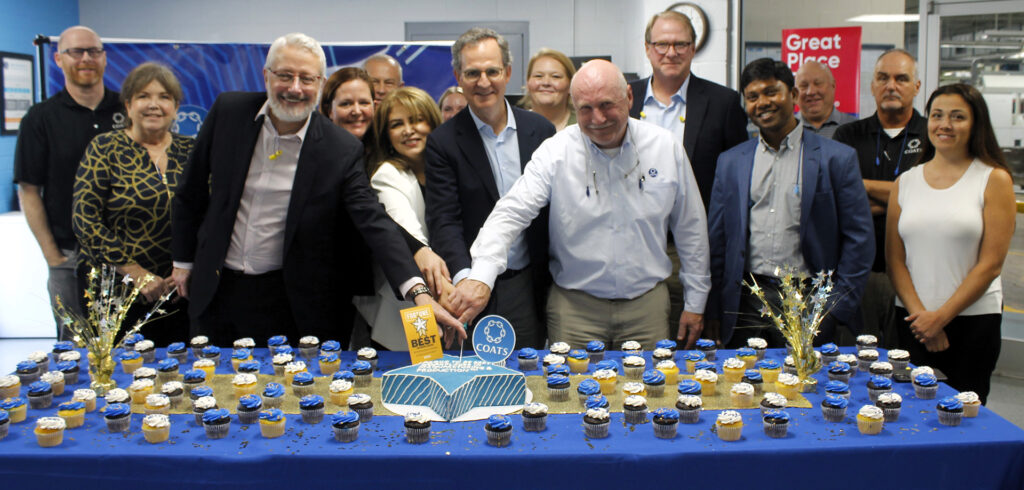
Coats Group has been recognised by Great Place to Work® and Fortune magazine as one of Fortune’s Best Workplaces in Manufacturing & Production™ 2024 in September. The Best Workplaces in Manufacturing & Production award is based on analysis of survey responses from over 96,000 current employees at Great Place To Work® Certified™ companies in the manufacturing and production industry.
The survey also considers the breadth and impact of company workplace programmes. Organisations are assessed on their efforts to create great workplaces and positively impact people and communities across multiple countries. Coats India, Honduras and UK were also named among the local Best Workplaces in Manufacturing & Production, reaffirming the successful impact of the company’s approach to culture.
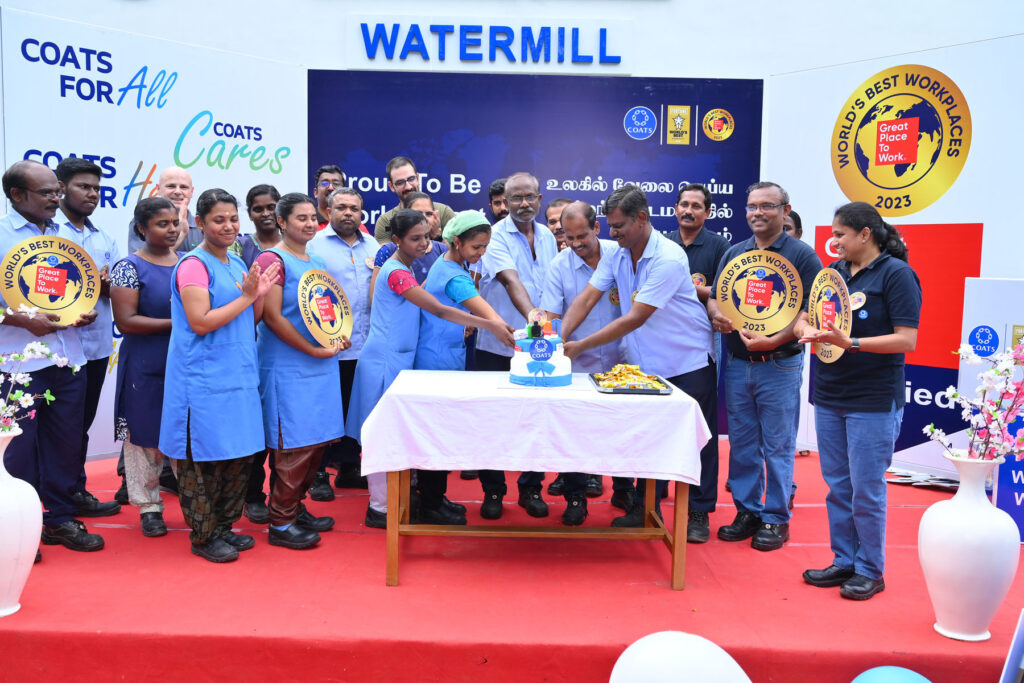
In 2024, Coats was also listed as one of UK’s Best Workplaces for Women and Coats Turkey listed as Best Workplaces for Innovation.
![]() | ![]() | ![]() | ![]() |
![]() | ![]() | ![]() | ![]() |
![]() | ![]() | ![]() | ![]() |
![]() | ![]() | ![]() | ![]() |
![]() | ![]() | ![]() | ![]() |
![]() | ![]() |