Composite reinforced tapes are an innovative, high tech solution with enhanced properties. Their advanced construction offers a higher, more optimal performance than traditional woven tapes.
In addition, they can be custom made for a customer using different types of high-performance fibres, each one helping to attain the required attributes of the end use application. These fibres are applied unidirectional with different types of coatings. The tape construction, a perfected coating system and an excellent extrusion procedure, ensure that the fibres are completely covered, thus guaranteeing an optimal performance.
Composite reinforcement tapes can be utilized in various applications such as reinforcement of submarine cables and pipes, both on-shore and offshore, as well as the automobile industry, just to name a few. One of the main applications is in flexible pipe risers used in the oil and gas industry.
Risers that bring undersea oil to the surface must be strong enough to resist the water pressure present at deep drilling depths as well as the turbulence that occurs on the surface surrounding the rigs and vessels they attach to.
To safely transport hydrocarbons from the ocean seabed to the surface, a pipe must combine both strength and flexibility. The strength requirements are needed mainly due to high internal fluid pressure as well as external hydrostatic pressure at large depths and tensile forces.
Flexibility is required because of the large motions a floating production platform will experience. These motions would inevitably result in yielding and structural failure of the pipe if it was rigid. The key to flexibility is the composite structure of the pipe cross section.
The basic components of the composite structure are:
- Armour layers
Intended to withstand pressure and tensile forces, they are usually made up of steel wires helically wound around the pipe axis. These layers carry most of the loading. - Polymer layers
Provide containment of the transported fluids, and prevent seawater from reaching the armor layers.
An unbounded flexible pipe structure is made of several layers, which are carefully preformed. These layers consist of helically wound metallic strips and armor wires combined with concentric layers of polymer, textile, and fabric tape as well as friction-reducing materials. To ensure a robust and uninterrupted service performance, it is paramount to select the material for each layer that best meets the given design conditions or end use attribute requirements.
Reinforced tape is used in one of the internal layers in order to avoid the birdcaging effect. The birdcaging failure occurs when the tensile armor bears a load, which it is not designed for. Tensile armors are not designed to withstand compression, and may fail by radial expansion or lateral buckling.
To provide extra support and help prevent the birdcage effect and lateral buckling, reinforcement tape can be wrapped around the tensile armor layers. By doing so the flexible pipe can maintain its structural integrity when under extreme external pressure.
Gotex Composite Reinforced Tape and Gotex Technical Woven Tapes are a solution to reinforce or repair pipes, ensuring they do not suffer from the birdcage effect, corrosion defects or mechanical damages. Instead of replacing a pipeline, which can be costly, these tapes can significantly improve operating costs because they can be rapidly installed, keep their integrity for a long period of time and require minimum maintenance.
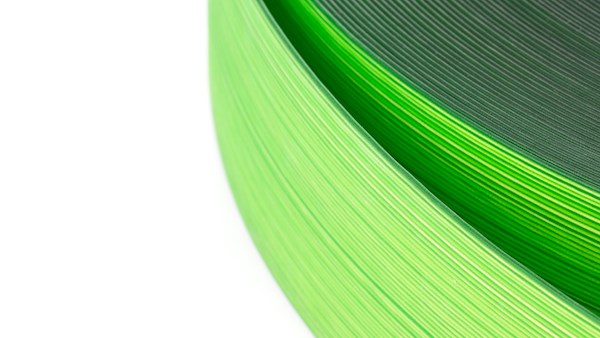
Gotex XTRU PE A
Gotex XTRU PE A es una cinta innovadora que fortalece y preserva la vida útil de las tuberías flexibles utilizadas en petróleo y gas.
Más información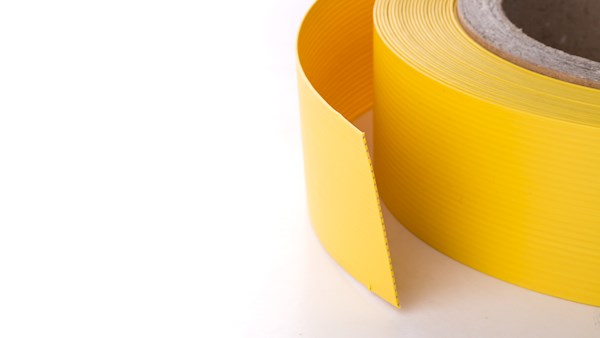
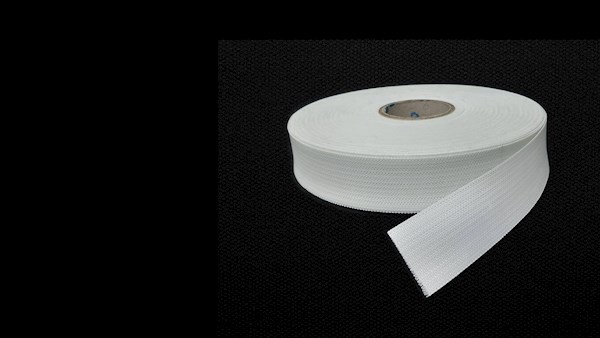
Gotex FG WT
A fibreglass woven tape used in telecommunications cables to prevent damage from rodents.
Más información