Sustainability Certifications
-
Registered users can place Bulk Orders . Contact local Coats office for registration.
Contents
Our aim at Coats is to make our own business activities as sustainable as possible and also to provide products and services that provide sustainable options to our customers and all subsequent users.
The textile supply chain is complex and multi-tiered, and we strongly believe that only by working together across networks of formal and informal groupings, can players in the supply chain significantly improve compliance standards and retain the industry’s licence to operate while also winning the competitive battle for consumers’ hearts and minds across the globe.
Managing precious resources wisely
Without water we could not make thread. Most of the water we use is in dyeing our products, but it’s also used to produce the raw materials we need and throughout the manufacturing process. It is a vital and shared resource and we need to make sure we use it efficiently, particularly as water is scarce in some parts of the world.
We have made considerable reductions in water consumption over recent years, achieving a reduction of 28% in the 6 years up to 2018, our new base line. We have committed to a higher rate of reduction over the next period up to 2022. In 2019 we achieved a reduction of 2% as we introduced and trained people on new approaches to water management that will facilitate increased reductions in the coming years.
These reductions will mainly be through changes to processes we use, but also through increasing awareness amongst our employees.
In all the new dyeing machines that we install, we are now able to dye with half the amount of water used in traditional machines, so as we replace old machines or expand capacity, we will utilise increasingly less water. We have also been developing new approaches that allow us to get some of those same benefits on existing machines.
We have also increased the amount of water we recycle, which now represents 24% of the total amount we use. For example, at our manufacturing unit in Sevier, in the US, we have started to recycle water discharged from the water-cooled air conditioning system saving 10% of the site’s total water use every year.
Renewables for sustainable future
The use of fossil fuels and the associated greenhouse gas emissions contribute to climate change. Climate change can potentially damage our business and the communities we serve, as global temperatures increase and weather patterns are affected. We clearly have a responsibility to reduce our contribution to this and thus help to mitigate these risks.
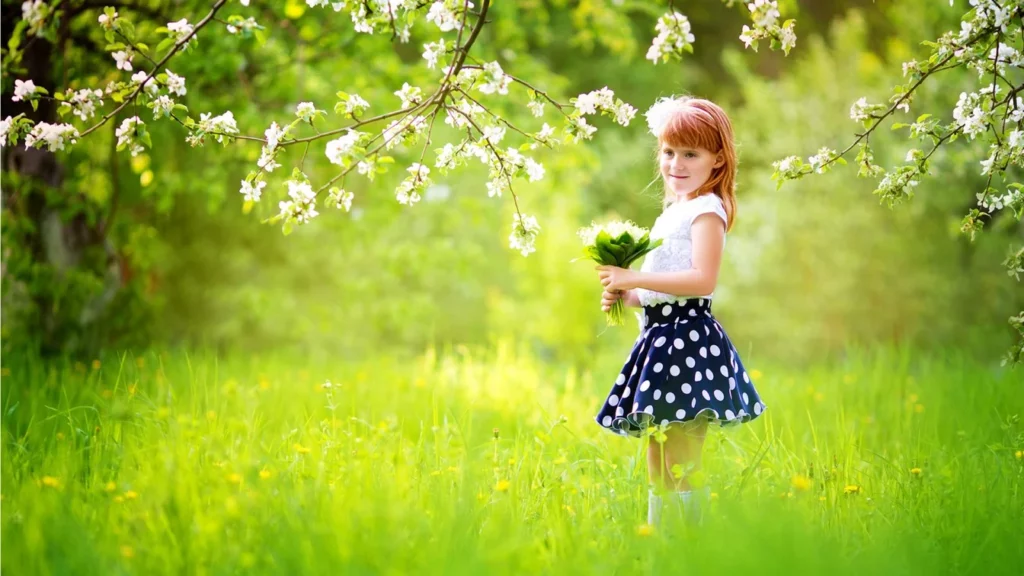
In the 6 years to 2018, our new base year, we reduced our total emissions by 19% while production increased, so our emissions intensity dropped by 25% over this period. In 2019, we generated 275 thousand tonnes of greenhouse gas emissions. This is a reduction of 3% compared to the same period the previous year, while production volumes dropped by 2%, so the net reduction in emissions intensity was 1%.
Our aim is to increasingly use renewable energy, mainly in the form of electricity. Last year, 32% of our energy mix was renewable.
Protecting our planet
To ensure sustainable growth, now and in the future, it is important that we use resources efficiently. We reduce, reuse and recycle our waste, using resources economically and limiting the disposal of waste to landfill.
Since 2018, we have been focusing on extending our waste reporting to include all areas of our business activities and to form the basis for our future reduction targets. In 2019, 9% of our purchased materials became waste of which 71% was reused or recycled.
Furthermore, we are increasingly using others’ waste to produce innovative new recycled products. For example, we manufacture our recycled EcoVerde threads from discarded plastic (PET) drinks bottles. Coats EcoVerde was the first globally available 100% recycled range of premium sewing threads on the market and offers the same proven level of performance as the industry’s leading non-recycled threads. The core products in this range were launched in 2018 so sales are currently small but demand is growing rapidly. We also manufacture recycled metal and plastic zips; Opti M EcoVerde and Opti S EcoVerde. We have also increased the use of recycled material in our product packaging and this now accounts for 60% of our packaging. We are also engaged in trials with customers to try to reduce the amount of packaging that we use for our products.
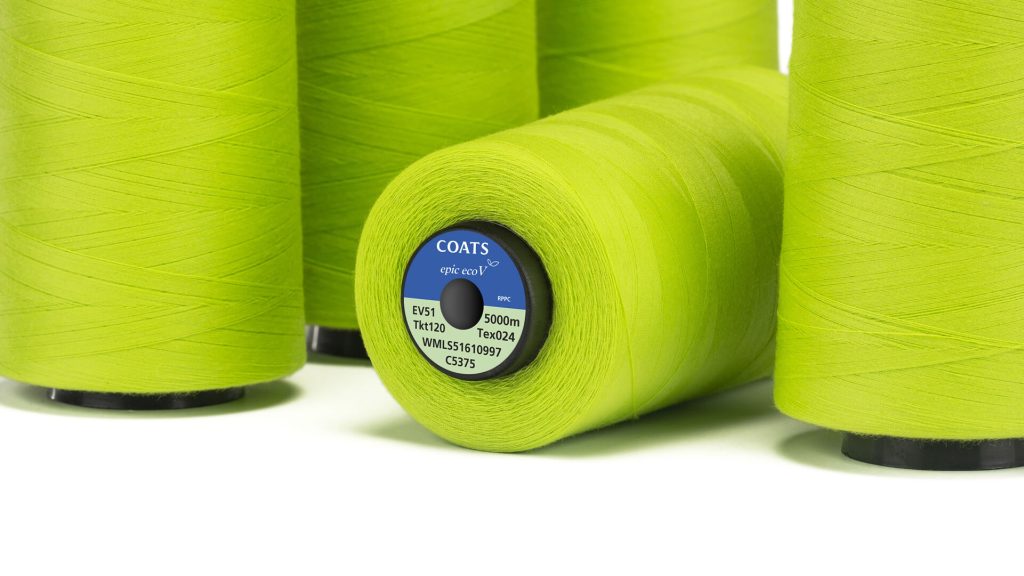
We also work closely with our customers to help them use more sustainable materials and reduce their waste. For example, we have developed advanced, high-performance thermoplastic products that are lightweight yet extremely strong for use in the automotive and aerospace industries, which can help reduce the weight of vehicles thus making them more efficient to run. These materials can be formed into the right shape and size, with virtually no waste, and they are also recyclable at end of life.
ZDHC
At Coats, we aim to ensure that the effluent that we discharge from our manufacturing facilities has minimal impact on the environment around our factories.
We are members of the Zero Discharge of Hazardous Chemicals (ZDHC) programme which aims to eliminate hazardous chemicals from the global textile, leather and apparel & footwear supply chains and ensure that effluent is properly treated. The programme’s vision is to have ZDHC guidelines and tools become the accepted industry standard.
Launched by six leading brands in 2011, the ZDHC Programme has since grown to 30 signatory brands and 123 contributors from the chemical industry, textile manufacturing and testing and accreditation laboratories Coats has joined as a Contributor in the Textile and Footwear industry.
We have robust programmes in place to ensure we always comply with local legislation. Although local legal requirements are becoming more and more stringent, weare going further, by investing in new technology to ensure that all of our effluent will meet ZDHC Wastewater guidelines by 2022. Over the past five years, we have spent or have committed to spend over $20 million on new effluent treatment plants and technology Projects include a zero liquid discharge plant in one of our largest facilities in India.
We have also started a programme to automate and enhance the testing of wastewater from our manufacturing sites. The new system automatically measures the water quality and triggers an alarm if any of the key parameters gets close to, or above, the limits we have set. This enables us to monitor wastewater quality in real time and decide what action to take to continuously ensure our compliance with required standards. We have also been successfully trialling a system that automatically blocks effluent discharge if key parameters are breached. Our aim is to progressively install this system across our units.
ZDHC have their own Manufacturing RSL which we ensure is included within our own Coats MRSL. Our acceptable limits are often much lower than the ZDHC MRSL limits, to ensure that we are fully compliant with customer expectations.
OEKO-TEX®
In recent times the world is much more focused on ecology.
Leading garment brands and retail chains worldwide which manufacture children’s clothing, bed linen and textiles worn next to the skin are promoting their products with STANDARD 100 by OEKO-TEX®, because it distinguishes ecologically safe textiles from textiles that contain or may contain harmful substances such as formaldehyde, heavy metals, pesticides, etc.
The principle objective of STANDARD 100 by OEKO-TEX® is to ensure that the certified products are not detrimental to human health, when in contact with the skin. The possession of a STANDARD 100 by OEKO-TEX® certificate has become a deciding factor when selecting suppliers for textile products.
At Coats, all of our apparel and footwear manufacturing facilities produce products that are STANDARD 100 by OEKO-TEX® Class I certified, the most stringent class covering textile items suitable for babies and toddlers.
The Origin of OEKO-TEX®
In the 1980’s, The Austrian Textile Research Institute in Vienna prescribed an innovative standard known as Austrian Textile Standard (OTN 100). Similarly in very early 1990’s, the Hohenstein Research Institute in Germany, renowned for its work in the field of clothing physiology, developed Hohenstein Eco Check. The combined experiences of these two pioneering institutions led to the creation of the International Association for Research and Testing in the field of Textile Ecology, also referred to as the International OEKO-TEX® Association.
Today, the International OEKO-TEX® Association is a group of 18 well-known textile research and test institutes with representative agencies and contact offices in over 70 countries worldwide and is responsible for testing harmful substances according to the STANDARD 100 by OEKO-TEX®.
STANDARD 100 by OEKO-TEX®
The STANDARD 100 by OEKO-TEX® is a globally-uniform testing and certification system for raw textile materials, intermediate and end products at all stages of processing, based on their ecological properties on humans. This standard includes an analysis of harmful substances, prescribing a scientifically determined limit value for each substance. The modular principle of OEKO-TEX® ensures that textile products at all stages of the processing chain are tested for harmful substances and certified accordingly.
The product label ‘Confidence in textiles’ is the most widespread and widely recognised international trademark in testing textiles for harmful substances.
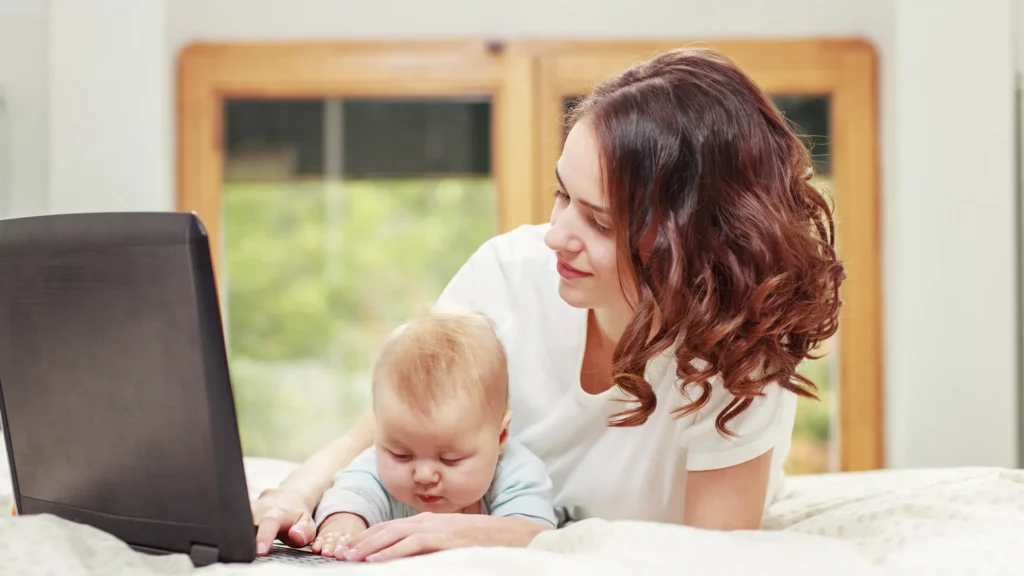
Substrates covered by STANDARD 100 by OEKO-TEX®
The STANDARD 100 by OEKO-TEX® covers all sewing and embroidery threads such as staple spun polyester, poly/poly-corespun, polyester/cotton corespun, trilobal polyester, continuous filament polyester, continuous filament texturised polyester and continuous filament nylon 6. The certificate also approves cotton threads for special applications and bonded threads for fusible or glazed versions of the above mentioned substrates for apparel, footwear and related industries.
Restricted Substances List (RSLs)
At Coats we are the leading thread manufacturer, and we believe our Coats Restricted Substance Lists (both our Products RSL and and our Manufacturing RSL) are the most stringent in the textile industry.
We take on board what our brands restricted substances are, so we ensure that our customers individual chemical requirements are met and included on the Coats RSL. Every year we are ensuring the most stringent of standards, as our customers’ lowest permitted chemical limits become our limits. When requested by our customers, we provide detailed safety data sheets, including the identification of hazardous chemicals for any of our products.
From our experience of interacting with brands, retailers and manufacturers across the world, it is clear that many industry players already have compliance high on their agendas and are investing to improve standards globally. There are many outstanding initiatives in action as, for example many companies are now committing to eliminate hazardous chemicals from their supply chains.
At Coats, we strongly believe that compliance adds sustainable value to our business and by extension, to our customers’ businesses. We are proud of our achievements to date and are committed to continuous improvement.
Product safety
We are committed to ensuring the safety of our end consumers when using our products. As a result we continually respond to feedback on product performance and continue to work with our suppliers to ensure the safety of our raw materials and product components.
Our aim is to maintain zero incidence of product safety related issues, and our goal is to successfully achieve that year on year. We continue to review the risks associated with our existing and new product lines and product safety is an important issue in new product development.
Coats’ Product Safety programme ensures that all products supplied to the customer are safe to use and do not contain any potentially allergenic or harmful substances. The programme is underpinned by rigorously enforcing our Coats MRSL.
Coats RSL
We maintain a Restricted Substances List (RSL) which incorporates the requirements of all the major internationally recognised environmental standards and legal regulations (for example REACH, Oeko-Tex, The State of California’s Proposition 65, CPSIA) as well as our customers’ and brands’ own restricted substances lists, and industry lists such as ZDHC and bluesign®. It extends to some 900 chemicals and all of our suppliers are required to comply with it. It is rigorously enforced. We believe that Coats Manufacturing Restricted Substances List (CMRSL) is the most comprehensive RSL in the textile industry and it has been referenced by other organisations as best practice. In 2019, we introduced an additional Restricted Substances List which is particularly applicable to packaging materials, following guidelines issued by the AFIRM Group. All suppliers of packaging and make-up materials must comply with the limits which are set out in this standard.
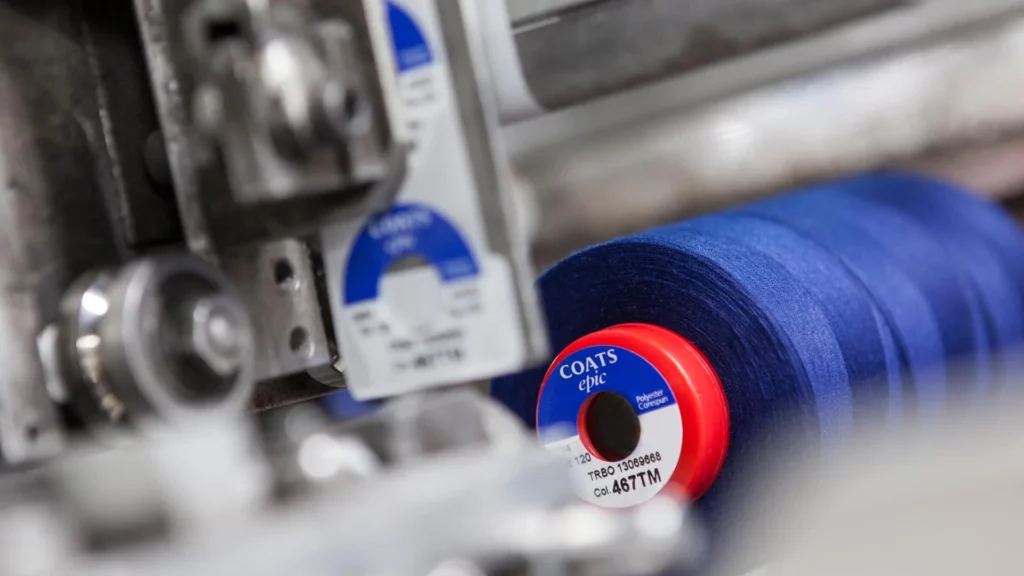
In 2012, we placed a ‘Usage ban’ in our CRSL on all of the 14 hazardous chemicals identified by ZDHC. These chemical groups are: AP & APEOs, Chlorobenzenes & Chlorotoluenes, Chlorophenols, Azo dyes, Carcinogenic dyes, Banned Disperse dyes, Flame retardants, Glycols, Halogenated solvents, Organotin compounds, Perfluorinated & polyfluorinated chemicals (PFCs), Phthalates, Poly aromatic hydrocarbons (PAHs) and Volatile organic compound (VOCs). We worked with our suppliers who used some of these substances in the production of our process chemicals to first of all identify them in their base chemicals and intermediates, and then systematically purge them from their supply chain.
For example, in June 2012 we found very low, but detectable levels of one of these ‘priority chemicals’ – an alkyl phenol ethoxylate (APEO) – on one of our thread products. APEOs, although commonly found in washing and cleaning products, are becoming banned since they are endocrine disruptors in humans and animals. Although the measured amount of APEO in this thread product was well below the current industry limits, we immediately tracked down the APEO source and worked with the raw material supplier to replace the non-compliant spin finish with an APEO-free alternative.
In 2014 we embarked on a project to replace all long chain perfluorinated chemicals (PFCs) used in our water resistant products with less harmful ‘C6’ perfluorinated chemicals. Extensive trials were carried out on a number of products to achieve optimal performance and with no deterioration after prolonged use. We completed the transition from C8 to C6-based PFCs before the end of Q3 2014, thus, we have eliminated from our supply chain all traces of two of the most persistent carcinogens associated with water resistant textile finishes – Perfluorooctanesulfonic acid (PFOS) and Perfluorooctanoic acid (PFOA). C6-based chemicals were replaced by C4-PFCs or non-PFC chemicals in 2017 and any remaining C4-PFC chemicals are now being phased out. A phased approach was adopted for the elimination of PFCs, as (i) the chemical industry took some time to respond to the need for fluorine-free, durable, anti-wick finishes and (ii) it was important that any performance differences in the end product were not observed by the end-user.
These are just some of the ways our CRSL is setting industry standards.
Better Cotton Initiative (BCI)
Better Cotton Initiative (BCI), a global not-for-profit, is the world's largest cotton sustainability programme.
BCI aims to transform cotton production worldwide, by addressing the negative impacts of cotton growing and processing. As a BCI member, Coats is part of a global community sharing in this commitment. Through its work with a diverse range of stakeholders across the supply chain, BCI promotes continuous improvements that are measurable for the environment, farming communities and the economies of cotton-producing areas. Under the following four aims, BCI is working towards making ‘Better Cotton’ a sustainable mainstream commodity:
- Reduce the environmental impact of cotton production
- Improve livelihoods and economic development in cotton producing areas
- Improve commitment to and flow of Better Cotton throughout supply chain
- Ensure the credibility and sustainability of the Better Cotton Initiative
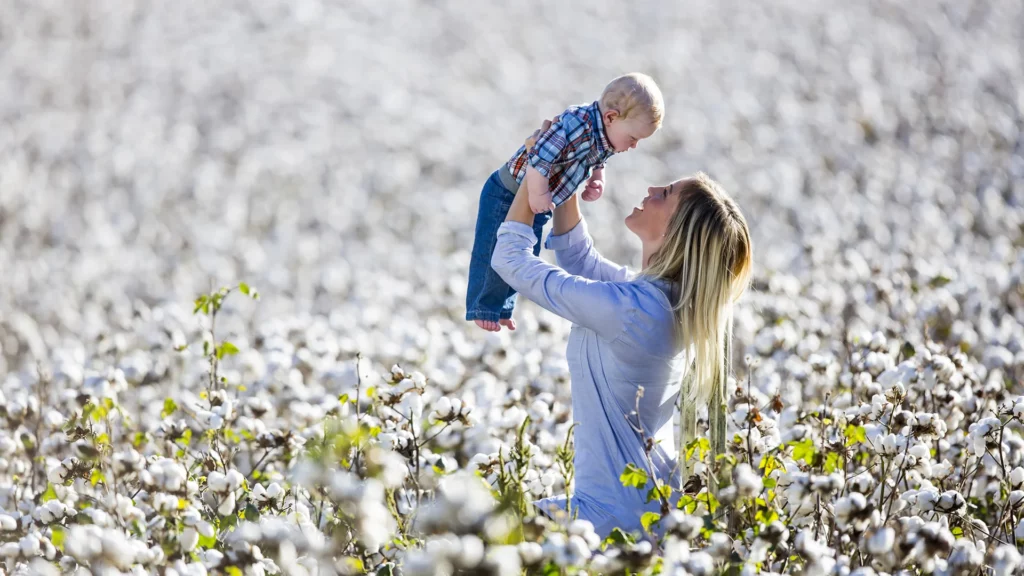
Coats Tre Cerchi Vero+ is Cradle to Cradle™ compliant for its dyes and chemicals.
Cradle to Cradle™ is a standard that ensures that finished products are designed and produced in such a way that the materials used in them can be treated appropriately at end of life, whether it be by recovery and recycling for non renewable materials or through biodegradation for renewable materials. Under this standard the dyes and chemicals in use have to be able to fit the needs of the end of life process for the product and hence have to be carefully chosen.
Global Recycle Standard
The Global Recycle Standard (GRS) was originally developed by Control Union Certifications in 2008 and ownership was passed to the Textile Exchange on 1 January 2011.
The GRS is an international, voluntary, full product standard that sets requirements for third-party certification of recycled content, chain of custody, social and environmental practices and chemical restrictions.
The GRS is intended to meet the needs of companies looking to verify the recycled content of their products (both finished and intermediate) and to verify responsible social, environmental and chemical practices in their production. The objectives of the GRS are to define requirements to ensure accurate content claims and good working conditions, and that harmful environmental and chemical impacts are minimised. This includes companies in ginning, spinning, weaving and knitting, dyeing and printing and stitching in more than 50 countries.
Coats ensures that any facility that processed recycled materials is externally certified to GRS, standards and that any recycled materials that we buy are certified so that we can provide fully certified recycled products.
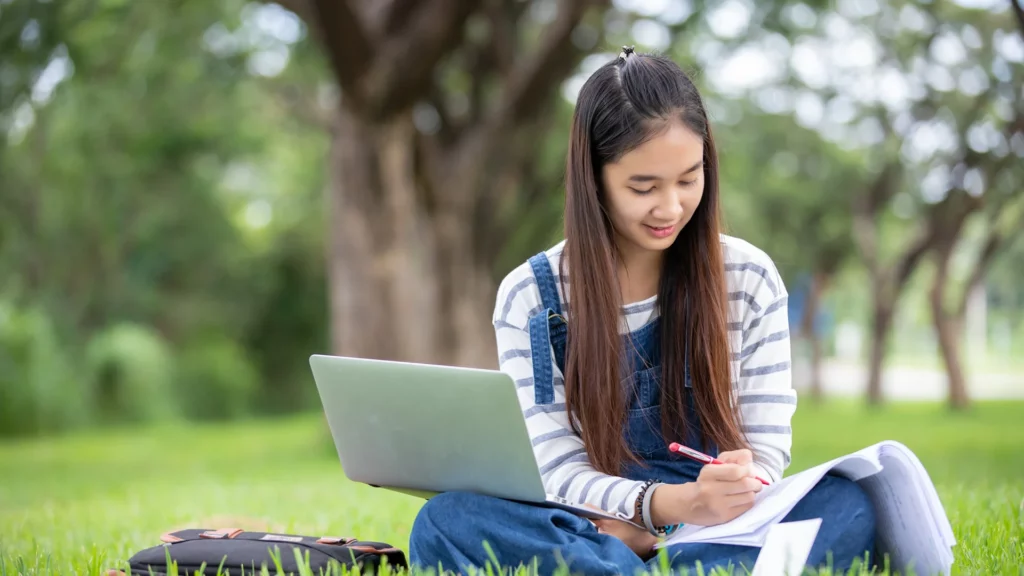
Global Organic Textile Standard (GOTS)
The Global Organic Textile Standard (GOTS) is an internationally recognised organic textile standard.
Since its introduction in 2006, GOTS has demonstrated its practical feasibility and is supported by the growth in consumption of organic fibres and the demand for unified processing criteria from the industry and retail sectors.
GOTS ensures the organic status of textiles from the harvesting of the raw materials through environmentally and socially responsible manufacturing all the way to labelling, in order to provide credible assurance to the consumer. The standard covers the processing, manufacturing, packaging, labelling, trading and distribution of all textiles made from at least 70 percent certified organic natural fibres. The final fibre products may include, but are not limited to, yarns, fabrics, clothes and home textiles.
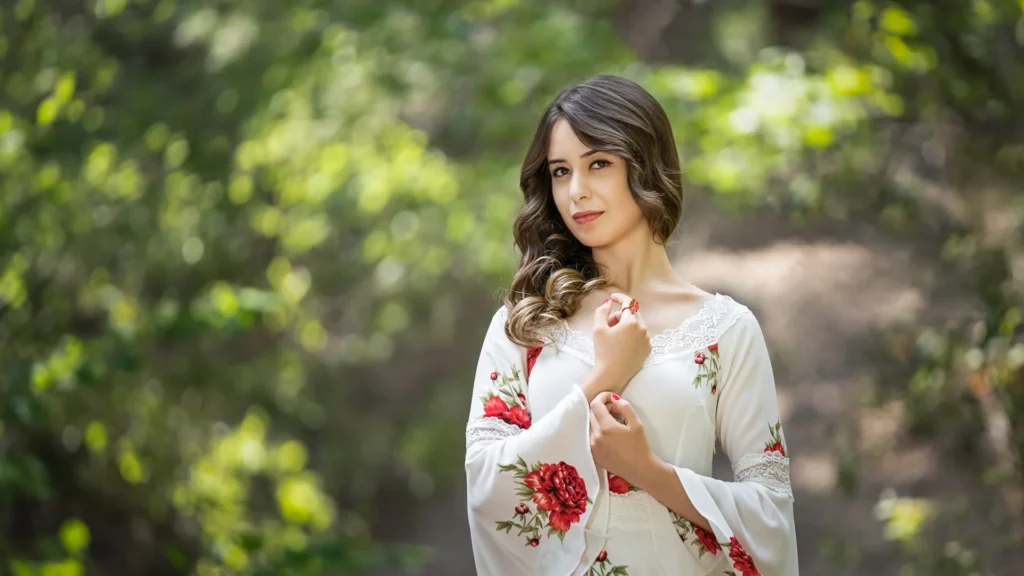
Higg Index
The Higg Index is a suite of tools, developed by the Sustainable Apparel Coalition.
Used to measure and score a company or product’s sustainability performance along the supply chain, the Higg Index provides businesses with a holistic approach towards making improvements for the environment as well as for the social wellbeing of factory workers and local communities.
The Higg Facility Environmental Module (Higg FEM) tool can be used to measure environmental performance at individual factories in a standardized way. Environmental management systems, energy use, greenhouse gas emissions, water use, wastewater, emissions to air (if applicable), waste management, and chemical use and management are measured. At Coats we are proud to say that in 2019, we used the Higg FEM across 11 of our sites already, and reports can be found on the Sustainable Apparel Coalition website. We intend to continue to roll out the Higg FEM across more of our production facilities and continue to make meaningful improvements in sustainability performance.
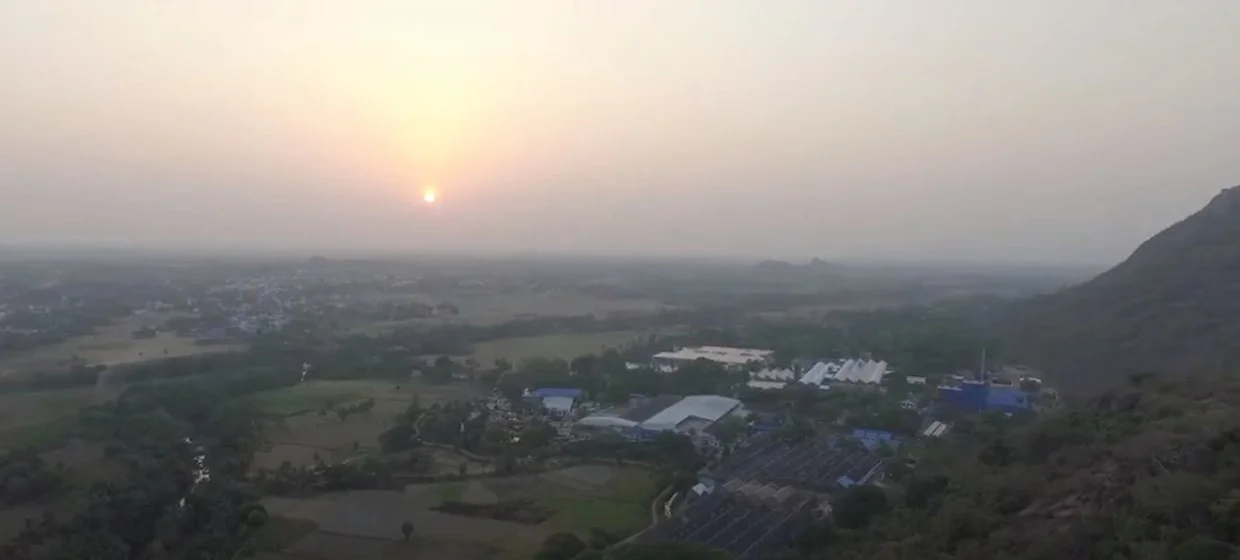
Great Place to Work
Great Place to Work® (GPTW) is the global authority on building, sustaining and recognising high-trust, high performance workplace cultures.
GPTW lead the industry with the most rigorous, data-based model for quantifying employee experience.
The GPTW organisation uses a combination of a trust survey and culture audit to assess whether the culture meets the criteria to be a certified ‘Great Place To Work’. The trust survey measures employee feedback by asking questions on five areas: credibility, respect, fairness, pride and camaraderie, while the culture audit measures what managers do by assessing the people practices at Coats.
Coats have worked with the GPTW organisation for a number of years in Brazil, and with the HR Asia team in Vietnam.
Our goal is to have the employees at all of our key sites covered by the ‘Great Place To Work’ accreditation, or equivalent award, by 2022, covering at least 80% of our employees. After putting the process on hold in 2020 because of the pandemic we restarted is in early 2021 and we are delighted that 14 countries have now been awarded the GPTW certification, ensuring that at the end of 2021, 83% (compared to 6% in 2020) of our employees are covered by the award, far exceeding our target for the year and delivering our 2022 target a year early.
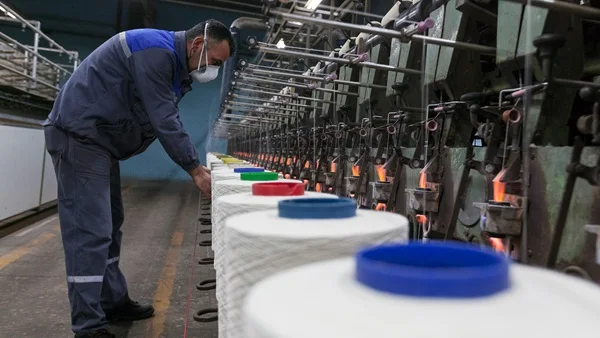