Materials
MATERIALS
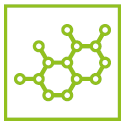
The materials we use to make our products are largely oil based and are energy intensive in terms of upstream production.
They are our main overall source of greenhouse gas emissions. Transitioning to materials with lower inherent emissions, by moving to recycled or bio-based materials is a priority to combat climate change.
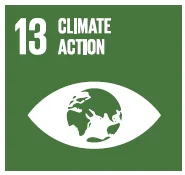
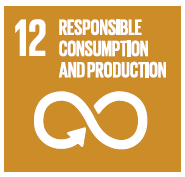
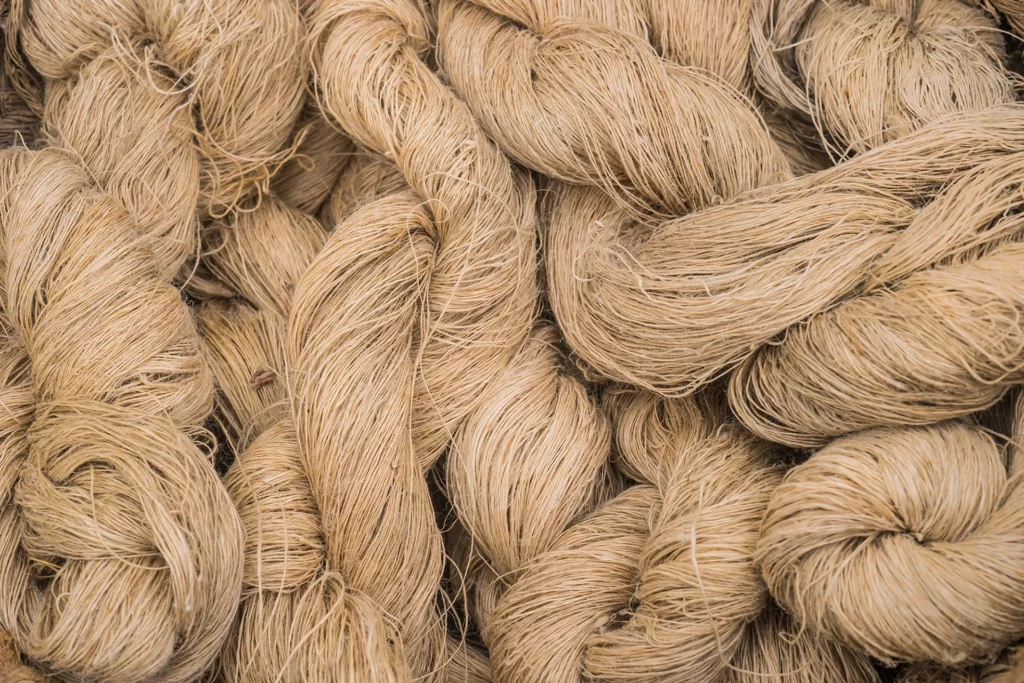
Plastic has typically been used in packaging of our products, both through incorporation of plastic sleeves to protect our product from dirt, dust and atmospheric contamination during transit and storage, and for the plastic thread supports onto which our product is wound for final use in sewing applications.
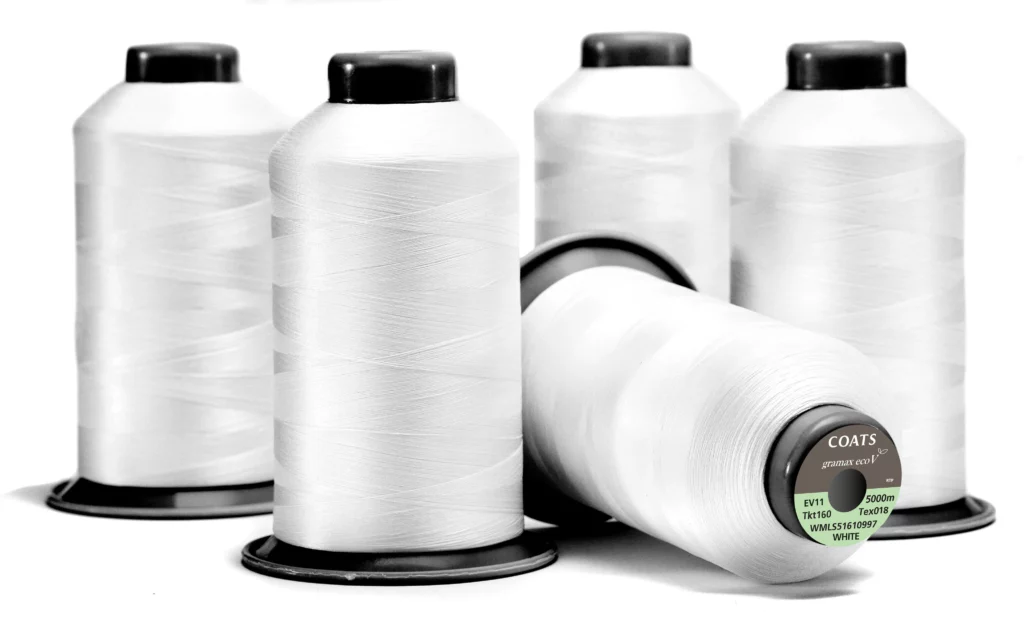
In 2022, we have eliminated use of 14.2 million plastic bags for packing finished goods, and have transitioned 36% of thread supports from virgin to recycled plastic.
How Composite Materials Create Value and Enable Sustainability
As an example, Coats EcoCycle is a ground breaking water dissolvable thread concept that helps facilitate end-of-life recycling when washed at 95°C. Whilst the thread maintains its quality, strength and durability during the life span of the garment, when exposed to a thermal washing process at temperatures above 95°C it allows the seam to dissolve so that non-textile and textile components can be easily separated for recycling. This product has the potential to be truly transformative in driving a circular textile economy. We are currently seeking to bring together the key industry players (e.g. brands, collectors and recyclers) to put the steps in place that are required in order for this solution to be scaled up. We are already working with our partners to explore how this might look in future.
NON-TEXTILE AND TEXTILE COMPONENTS CAN BE EASILY SEPARATED FOR RECYCLING
Our Performance Materials Division is focussed on development of innovative composites solutions which support the rapidly changing application areas in telecoms infrastructure, energy pipes, automotive and sporting industries. These industries are increasingly aiming to deliver light weighting of products without loss of technical performance.
In Automotive, the industry is implementing cost effective light weighting as a means to increase fuel efficiency, delivering significant reductions in full life cycle carbon emissions.
Composite solutions have many benefits for the transport industry, especially when compared to alternative materials such as metals.
They are far more lightweight therefore improving fuel efficiency, and can be engineered to be far stronger than aluminium or steel meaning that they maintain great strength relative to weight. Furthermore, they are flexible by design due to their ability to be easily moulded into complicated shapes with almost zero waste.
Coats highly innovative new technologies, Synergex™ and Lattice™, allow us to offer the industry a cost effective means to reduce weight beyond what is achievable through aluminium, magnesium and conventional carbon fibre and hybrid technologies. Synergex™ is a technology that commingles dissimilar fibres, thereby tailoring the fibre mix to the performance and cost needs of a specific application. Lattice™ is technology that allows us to place the fibre in a position and direction that is required by a specific application.
“We continue to work with our industry partners to further develop our innovations and we will lead with sustainability as the key focus in our composite expansion”
Through 2022 we continued our collaboration with a team led by General Motors, using our Lattice technologies to develop a tailored fibre-reinforced composite technology to aid development of lightweight, high performance and cost-effective structural battery enclosures for use in Electric Vehicles.
We continue to work with our industry partners to further develop our innovations and we will lead with sustainability as the key focus in our composite expansion, exploring future opportunities in thermoplastics, wind, hydrogen storage and EV technologies.
“Texon and Rhenoflex produce sheet materials or individual pieces that are largely undyed as they are hidden in the shoe construction”
During the acquisition processes for Texon and Rhenoflex we spend a lot of time assessing their sustainability strategies and performance and comparing it to Coats. Coats main business is producing threads and dyeing is the major process in terms of sustainability impact. Texon and Rhenoflex produce sheet materials or individual pieces that are largely undyed as they are hidden in the shoe construction. The core processes are producing synthetic or cellulosic sheets and impregnating or coating them, or using additive manufacturing techniques to produce sintered individual reinforcement pieces. Water use is far less intensive than in the Coats processes. Energy use is significant and is more geared towards Scope 1 heat energy than is the case for Coats.
Operational emissions reduction through energy efficiencies and transition to renewables is a high priority for both businesses. Material transition is a major area of focus and is well advanced in both companies. People-related issues are very similar to those in Coats.
Our conclusion from this review is that both acquired companies have a very similar approach to sustainability as Coats, and that while the balance of material issues varies between the entities the new acquisitions can be easily integrated into the Coats sustainability strategy framework.
Rhenoflex Multizone enables customized production of shoe caps with tailor made curing zones. We distinguish between two different versions: Multizone 1C allows for the production of different thicknesses of a material for a reinforcement cap while Multizone 2C makes it possible to combine different materials in a single reinforcement cap. The reinforcement material is hard where it needs to provide support, soft where it needs to be comfortable. This increases the performance and comfort of the shoe and also allows for the customized implementation of new ideas, shapes and designs as well as the integration of RFID (Radio- Frequency Identification) and NFC (Near Field Communication) chips. With its new Multizone process , we can reduce the weight of products by up to 25%. Multizone reinforcement solutions are thus particularly well suited to running shoes, as every gram counts for runners. Various patent applications for Multizone products and processes are currently under review. Rhenoflex always has in mind its goal of ensuring that an innovation in materials and/or production processes must be more sustainable than its existing equivalent.
As well as the reduction in carbon impact of the components themselves, additional carbon benefits come from us only shipping the customer useable material, reducing the impact of transportation and associated emissions by up to 50%. Our customers have no materials waste to manage and our production process has two labour intensive practices (cutting and skiving) completely eliminated, further saving on process energy. This highlights how a combination of materials and process innovation can deliver added unseen benefits and shows how we not only want to be as sustainable as we can, but to also pass on this benefit to our customers, to work together for a greener, cleaner future in footwear.
Footwear Components
In a market that is traditionally defined by materialintensive production processes, high waste generation and energy consumption, our 2022 footwear components acquisitions are known for pioneering sustainable production processes and eliminating waste. As far back as 1985, Rhenoflex already patented a process for manufacturing shoe reinforcement materials that was virtually 100% waste-free. At the time, Rhenoprint™ revolutionized the industry and has been continuously developed since then.
Rhenoprint™ Process
Zero Waste Production
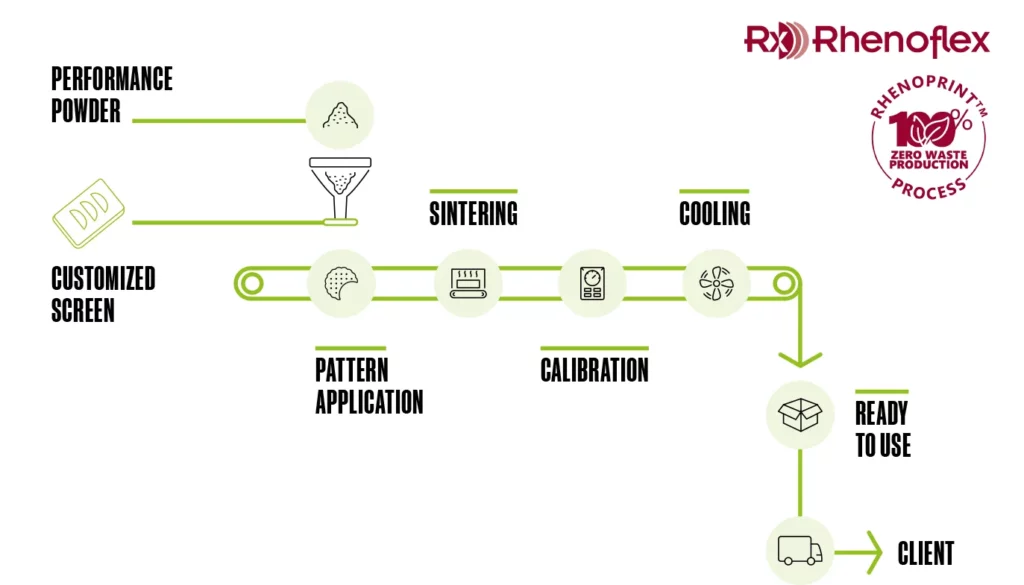
The prevailing industry standard for producers of footwear components is the use of so-called sheets, from which reinforcement materials are cut out. The starting point is impregnated, laminated, extruded or powder-sintered plastic panels and/or rolls of material. Available in different grades, they are made of a variety of raw materials and are used to punch or cut out reinforcement components (e.g. toe caps and heel counters). The punching and cutting process is an additional process step that consumes energy and takes time. This process can immediately produce thermoplastic caps by “printing” ready-to-use shapes that are adapted to customer requirements down to the last millimeter.
With RhenoprintTM the customary punching and cutting of sheet product become obsolete. This unique production process features a 50% lower CO2 footprint than traditional comparable processes. The resource-efficient, waste-free process continues to be state-of-the-art to this day, however our teams have delivered further innovations and developed the next generation of Rhenoprint™, which we market as Multizone.
Our recently acquired business, Texon has had a long standing commitment to diversifying its raw materials base and today source 70% of their polyester fibre from renewable sources. This transition towards eco materials has significantly lowered the CO2 impact of their footwear components product portfolio as well as helping to keep our natural environment free of potential pollution.
Over the last 18 months, the team has worked hard, in conjunction with their supply chain partners to validate new recycled alternatives, in particular for low fibre melt and spun lace backers.
In line with customer expectations, the footwear team are now extremely proud to offer a range of 100% recycled polyester structural solutions whilst still maintaining the key performance characteristics that Texon has prided itself on. Through 2023 further work will be delivered to completely phase out the use of any virgin polyester in their structural components products.
Coats Global Circularity
Our product specifications across all of our ranges are established to ensure fit-for-purpose products that are not over-engineered for the planned end use. This means that we do not produce or sell more material than that which is required by our customers. We also focus on ensuring that indirect material usage is minimised, which is especially important in the area of packaging as both the materials we buy and the products we sell require packaging to protect them during transport and storage. We address this upstream with our material suppliers and downstream with our customers, working collaboratively to find ways to minimise packaging and, where still deemed necessary, we strive to ensure that it can be reused or recycled.
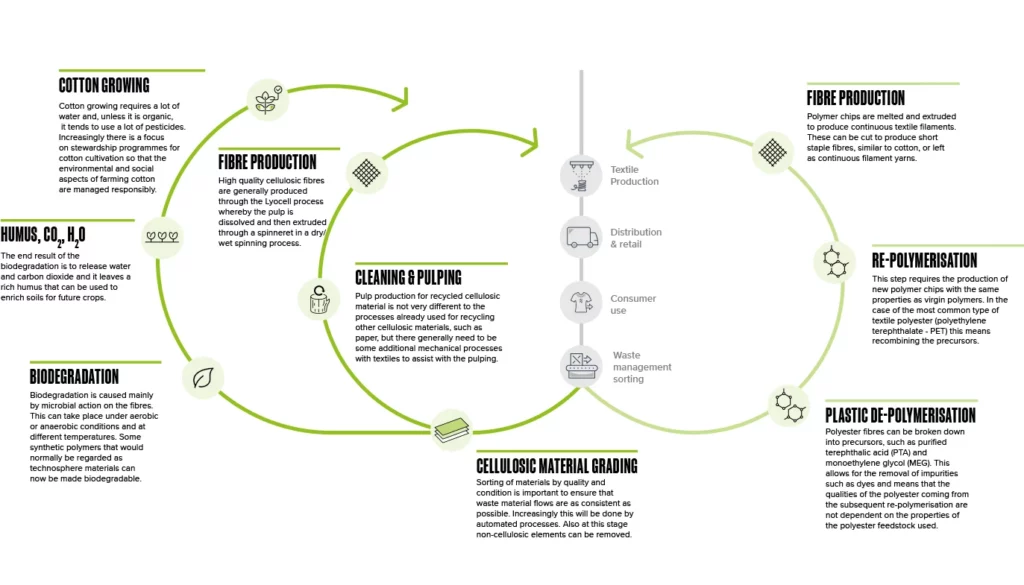
Materials: 60% volume free from new oil extraction raw materials
Indicator
|
Unit | 2022* | 2021 restated1 | 2021 | 2020 restated1 | 2020 | 2019 restated1 | 2019 | 2018 restated1 | 2018 |
---|---|---|---|---|---|---|---|---|---|---|
% of sustainable raw materials
|
% | 11% | ||||||||
% premium polyester sales from recycled material
|
% | 23% | 19% | 13% | ||||||
Total materials purchased by Coats
|
Tonnes | 107,052 | 133,062 | 115,302 | 144,802 | 139,399 | ||||
Process chemicals used
|
Tonnes | 13,577 | 17,101 | 13,820 | 16,034 | 18,213 | ||||
Packaging materials used
|
Tonnes | 23,878 | 22,482 | 22,486 | 24,077 | 27,062 | ||||
Materials used in Coats products
|
Tonnes | 73,010 | 93,479 | 78,996 | 104,691 | 94,125 | ||||
Textile fibres used in Coats products
|
Tonnes | 69,045 | 88,536 | 74,942 | 99,880 | 89,329 | ||||
Dyes and chemicals used in Coats products
|
Tonnes | 3,965 | 4,943 | 4,054 | 4,811 | 4,796 |
1Due to the sale of our Brazilian and Argentinian businesses in 2022 all years from 2018 to 2022 have been restated to exclude these businesses.
*2022 Data – All data excludes Brazil/Argentina, except emissions data, H&S data and economic value data.
For more information on our historical performance, please download Performance Summary Data
Energy: 22% reduction in Scopes 1&2 CO2e emissions
Indicator
|
Unit | 2017 | 2016 | 2015 | 2014 |
---|---|---|---|---|---|
Total materials purchased by Coats
|
Tonnes | 138,589 | 146,394 | 136,249 | 132,694 |
Materials used in Coats products
|
Tonnes | 93,268 | 95,261 | 90,444 | 87,002 |
For more information on our historical performance, please download Performance Summary Data